Building new wheels up
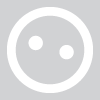
Matthewfalle
Posts: 17,380
Morning all, a daft question from a newbie!
I need to change the hub/freewheel on an American Classic Victory rear wheel (its on the foul weather/turbo bike so minimal - if any - budget spend). I've also never done this before but have always been intrigued so fancy giving it a go (I'm pretty confident with the spanners so happy to give it a go).
The freewheel is coming away from the hub so its shot.
Counting the spokes, its a 27 spoker- 13 non drive side, 14 drive side)
I presume that its just a case of finding a 27 spoke rear hub, unlacing the spokes transferring old knackered hub to the bin, lacing in new hub then truing up?
Simple as or am I missing something?
Also, I can find loads f 32 and 36 hole hubs but a dearth of 27s - is this because its an older wheel and is going to be a bind to sort? Anyone know of anywhere?
I've also posted this in workshop so if the mods think that one needs deleting then no problem at all.
Thank you in advance.
I need to change the hub/freewheel on an American Classic Victory rear wheel (its on the foul weather/turbo bike so minimal - if any - budget spend). I've also never done this before but have always been intrigued so fancy giving it a go (I'm pretty confident with the spanners so happy to give it a go).
The freewheel is coming away from the hub so its shot.
Counting the spokes, its a 27 spoker- 13 non drive side, 14 drive side)
I presume that its just a case of finding a 27 spoke rear hub, unlacing the spokes transferring old knackered hub to the bin, lacing in new hub then truing up?
Simple as or am I missing something?
Also, I can find loads f 32 and 36 hole hubs but a dearth of 27s - is this because its an older wheel and is going to be a bind to sort? Anyone know of anywhere?
I've also posted this in workshop so if the mods think that one needs deleting then no problem at all.
Thank you in advance.
Postby team47b » Sun Jun 28, 2015 11:53 am
De Sisti wrote:
This is one of the silliest threads I've come across.
Recognition at last Matthew, well done!, a justified honour
De Sisti wrote:
This is one of the silliest threads I've come across.

Recognition at last Matthew, well done!, a justified honour

smithy21 wrote:
He's right you know.
0
Comments
-
It's 28, count again!left the forum March 20230
-
You are correct Sir! My bad.
Any ideas re hubs as you seem to be pretty darn hot on this stuff? Google is producing nothing except Chris King etc at big money. I must admit that I would have expected Tiagra/Sora to be available through the usual suspects but they are all 32/36 hole.Postby team47b » Sun Jun 28, 2015 11:53 am
De Sisti wrote:
This is one of the silliest threads I've come across.
Recognition at last Matthew, well done!, a justified honoursmithy21 wrote:
He's right you know.0 -
If you want to do a good job you need to invest in some basic tools.
My advice is to simply replace the freehub if that is the problem, or the bearings if need be... I am not quite sure why you want to rebuild the wheel on a new hub. I like to think it's a bit more complicated than you anticipateleft the forum March 20230 -
ugo.santalucia wrote:If you want to do a good job you need to invest in some basic tools.
or invest some time in making friends...how's the build going Paolo?:shock:
WyndyMilla Massive Attack | Rourke 953 | Condor Italia 531 Pro | Boardman CX Pro | DT Swiss RR440 Tubeless Wheels
Find me on Strava0 -
Hi Ugo
Hub sorted (new) for next to nothing, so in budget! Re tools - yup, agree: as its (at the moment) a one off I'm going to look for something cheap and if I get the wheel building bug then I'll look to invest.
Am looking at new hub as the bearings are tired (to say the least) as well so to me a new hub/freewheel for £3 is probably less than I can get the bearings alone for.
I'm not expecting a world beater for what I've paid for the hub but if it gets the bike back on the trainer then its a deal.
I must admit that its more of an intrigue thing at the moment - something I've always looked at doing but never got around to it - I'll keep you posted as it goes along.
Thanks again for your postsPostby team47b » Sun Jun 28, 2015 11:53 am
De Sisti wrote:
This is one of the silliest threads I've come across.
Recognition at last Matthew, well done!, a justified honoursmithy21 wrote:
He's right you know.0 -
Matthewfalle wrote:Am looking at new hub as the bearings are tired (to say the least) as well so to me a new hub/freewheel for £3 is probably less than I can get the bearings alone for.
Clearly you have lost the plot re. the budget if you think you can get a new hub for 3 pounds. The idea of rebuilding a wheel instead of replacing two bearings is bonkers to say the least. I will stop posting now before losing my patience... :xleft the forum March 20230 -
drlodge wrote:ugo.santalucia wrote:If you want to do a good job you need to invest in some basic tools.
or invest some time in making friends...how's the build going Paolo?:shock:
Doneleft the forum March 20230 -
ugo.santalucia wrote:Matthewfalle wrote:Am looking at new hub as the bearings are tired (to say the least) as well so to me a new hub/freewheel for £3 is probably less than I can get the bearings alone for.
Clearly you have lost the plot re. the budget if you think you can get a new hub for 3 pounds. The idea of rebuilding a wheel instead of replacing two bearings is bonkers to say the least. I will stop posting now before losing my patience... :x
Sorted off Ebay already from some shop in Gloucester with a 99.8% good rating, plus a fiver postage. If it works it works, if it doesn't then its only £8 gone plus a bit of intrigue in the garage. Add on a couple of beers while I scratch my head over it.........
Worst comes to the worst I'll still have the original hub to pop on a new freewheel/bearings.......Postby team47b » Sun Jun 28, 2015 11:53 am
De Sisti wrote:
This is one of the silliest threads I've come across.
Recognition at last Matthew, well done!, a justified honoursmithy21 wrote:
He's right you know.0 -
Seems Ugo hasn't frightened you off, so all I can do is suggest you take plenty of photos of the wheel / lacing before you take it to bits, and possibly number the spokes so they go in the same places? And if the hub's knackered, are you sure the rim is worth re-using?0
-
Unless the new hub has the exact same dimensions as the old one it's likely you'll need new spokes of the correct length. You've probably got leeway of a few mm in spoke length but not much more.
Built a few wheels myself and it is deceptively easy (the hardest part is the spoke length calculation!) though I'm not sure I'd attempt it without at a truing stand at the very least.0 -
Thank you Plet and Keef - very much appreciated - very good tips. Must admit that to get a wheel to a certain standard - ie good enough for a turbo, not a £600 hand built race wheel) does seem to be deceptively easy, but hey, only time will tell.
This will be the first wheel build and, if it all goes wrong, then I've only wasted an afternoon and £8 (I'll probably be able to resell the hub for what I paid for it back on Fleabay anyway).
The rim is fine, its just the freewheel falling of the hub that goosed the wheel - I also need to down space it from its current 9/10 speed to 7 speed to match the 7 speed gruppo on the turbo bike so this will save me either the £3 for the kit off Wiggle or scrabbling about in the workshop for cassette spacers to downsize it all with.
A tip I have had off a mechanic friend is if you don't have a truing stand then pop the wheel in an old set of forks, pop the stem in a vice and go from there - won't be as specific as a truing stand but will be pretty darn on for a turbo bike with no rear brake.
Both wheels cost me nothing as well and are nice and clean, so hopefully this is all a go - go. Otherwise stuff it, I'll throw some Lightweights on there in a fit of pique and ragePostby team47b » Sun Jun 28, 2015 11:53 am
De Sisti wrote:
This is one of the silliest threads I've come across.
Recognition at last Matthew, well done!, a justified honoursmithy21 wrote:
He's right you know.0 -
Matthewfalle wrote:
A tip I have had off a mechanic friend is if you don't have a truing stand then pop the wheel in an old set of forks, pop the stem in a vice and go from there - won't be as specific as a truing stand but will be pretty darn on for a turbo bike with no rear brake.
If you can fit a rear hub in a set of forks I'll give you a 20 pounds note...
Before truing, you have to disassemble the wheel, I would start by reading how to fish the nipples out of a rim with no eyelets without dropping them inside the rim, which is a good starting point...left the forum March 20230 -
ugo.santalucia wrote:If you can fit a rear hub in a set of forks I'll give you a 20 pounds note...
I claim my prize: http://salsacycles.com/components/categ ... abler_fork0 -
Can I have half of the £20 as it was my post that prompted the whole shebang?Postby team47b » Sun Jun 28, 2015 11:53 am
De Sisti wrote:
This is one of the silliest threads I've come across.
Recognition at last Matthew, well done!, a justified honoursmithy21 wrote:
He's right you know.0 -
Matthewfalle wrote:Can I have half of the £20 as it was my post that prompted the whole shebang?
The problem is that you don't know what you are doing and instead of doing some reading, you want to go ahead... which is fine as an exercise of bashing and banging, but your plan has too many flaws to actually succeed... some have been highlighted, some you will find out as you build and some you will only find out when you actually ride the wheel if you wish to do so.
If you want to learn to build a wheel, this is the worst way of getting started, as using mismatched components will lead to inevitable frustration... spokes too short? You can't lace the wheel... spokes too long? You can't tension the wheel. Moreover, the spokes are bladed and well over 2.5 mm wide and they won't fit through a regular hub hole... is the hub you bought slotted? if not, are you going to slot it? Will you cut the slots in the correct direction to avoid the flange opening up like a tin of sardines while you are riding?
Unfortunately all this knowledge which you do need cannot be summed up in a forum post, not even in a forum thread... so you'll have to learn from your (many) mistakes... but good luck, happy to be proved wrong...left the forum March 20230 -
Hi Ugo
Thank you for the post - much appreciated: learning as I go here!
The existing spokes are round, not aero, so I've bought a hub to match. I must admit that I've taken a gamble on spoke length but as this exercise has only cost £8 so far I don't mind spending another tenner or so if the spokes aren't right. The minute it reaches £30 then its game over.
I'll be happy (and somewhat surprised!) if it all goes right first time around but my view on it is that if you don't give it a go at minimal cost you'll never know - at the least its a very inexpensive way of trying something - if I had spent £200 on a Chris King hub and tried to do this then that would have been a bit silly.
I've always found that the only way to learn most things is to give it a go and with a bit of time and patience - goes for mechanical as well as cerebral matters! I'll keep you updated so you can mock/stand back in awe (as seen fit at the time).Postby team47b » Sun Jun 28, 2015 11:53 am
De Sisti wrote:
This is one of the silliest threads I've come across.
Recognition at last Matthew, well done!, a justified honoursmithy21 wrote:
He's right you know.0 -
You can do this NOW - before you get any of the new parts....
Draw a detailed picture of how the wheel is currently laced. The key starting point is the spokes next to the valve hole.
Are the current spokes 'old style' J-bend, with round holes in the hub flanges? Those are easily available and fairly inexpensive.
Pay special attention to whether the 'heads' of the spokes are on the outside or inside of the rim.
And be sure to note which spokes are laced 'over' and 'under' where they cross each other.
Getting spokes of the proper length might be confusing, but I'm sure you can get good advice here when you know eactly what hub & rib will be used.
After the wheel is fully laced and preliminary spoke tighening is done, mounting the wheel in the frame will be adequate - downside is that finding a comfortable work position will be difficult.
Regarding spoke tension - do 'finger tests' of your current wheel with same number of spokes to develop an 'educated feel' for the tension on a working wheel. A similar tension on the new wheel should be OK.
If you choose to use some sort of tension gage, that's fine.
Building a functional wheel might take a while, but it is certainly possible for a DIY mechanic - especially since you don't have to be concerned with your 'labor rate'.
Jay Kosta
Endwell NY USA0 -
Hi,
A good tip, run a length of masking tape all the way around the wheel at approximately mid way along the spokes length to link them all together.
Remove all the nipples and separate the rim from the hub and spokes.
One by one, transfer the spokes to the new hub in the same pattern you are removing them from the old.
Be mindful that the hub doesn't quite sit centered in the rim. Its offset towards the non drive side (see pic below) to allow the wheel to be centered when the freehub is on. You can familiarize yourself with the good wheel before stripping it though.0 -
Brilliant stuff - cheers guys, thank you very much!Postby team47b » Sun Jun 28, 2015 11:53 am
De Sisti wrote:
This is one of the silliest threads I've come across.
Recognition at last Matthew, well done!, a justified honoursmithy21 wrote:
He's right you know.0 -
Brief update on today's happenings:
Having looked at ways of securing the wheel so that it still spins and can be trued up without having to clamp the bike in the work stand, I went down the dump, picked up an old frame for nothing, went home, cut the rear end off using an angle grinder (6 minutes), tidied up the cuts with the bench grinder (30 seconds) and now have a rudimentary wheel truing stand in the vice with a perfectly held rotating rear wheel with 360 degree access in a lovely shade of metallic British Racing Green.
Cost: About 20p in WD that was used to clean off new "stand" to make it smart and spotless.
Perfecto.
Right, bring on the hubPostby team47b » Sun Jun 28, 2015 11:53 am
De Sisti wrote:
This is one of the silliest threads I've come across.
Recognition at last Matthew, well done!, a justified honoursmithy21 wrote:
He's right you know.0 -
Nice one!
Just made one out of a bit of wood and aluminium plate, only clamps on the one side but plenty good enough to get it within a couple of thou.
It goes onto the workmate so I can work in the kitchen.
Need to get my ears calibrated so I can tension the spokes properly.0 -
Cheers dude - seems like we can't be stopped - excellent to hear of someone else who likes a challenge.
I've also noticed that the Park Tools one at PBK has a caliper for exact truing - nothing a couple of self tappers (pointy edge important for exactness) threaded through the stand and held in place with Loctite after being measured with vernier calipers won't solve.
Cost@ oooooh, nothing but 15 minutes with a drill and some calipers.
Job jobbed my son
6wheels: keep us updated on how you progress - intrigued to hear.Postby team47b » Sun Jun 28, 2015 11:53 am
De Sisti wrote:
This is one of the silliest threads I've come across.
Recognition at last Matthew, well done!, a justified honoursmithy21 wrote:
He's right you know.0 -
But first 'test' your new 'truing stand' with the old wheel, and MARK the stand somehow so you know where the center of the rim is supposed to be.
Use 'lock nuts' to adjust the indicators - that way you can accommodate other rim dimensions, or a severely out-of-true rim.
The goal is to have the finished wheel work properly on your BIKE!
Jay Kosta
Endwell NY USA0 -
Thanks Jay - good points. Agree completely re end goals
I'm going for light/medium weight Loctite so they can be adjusted easily but are held nicely in place - I build race motorbikes as an aside to the day job (political speech writer of all things...) and know that using the strong hold stuff can be a pain to release sometimes!Postby team47b » Sun Jun 28, 2015 11:53 am
De Sisti wrote:
This is one of the silliest threads I've come across.
Recognition at last Matthew, well done!, a justified honoursmithy21 wrote:
He's right you know.0 -
Matthew,
Don't know about a challenge, more of just being tight. Actually, because I will probably only build a set every year, spending money on stands and tension meters seems a waste. So for me, it's elastic bands and rulers, with the vernier measuring up a few feeler gauges for ultimate accuracy. :?
I'll be updating as and when, probably do the front wheel next week.
Trying to work out which party, I think you must be a Con man.0 -
A dishing tool is just a straight edge that you use to measure the relative position of the hub lock nuts to the rim. You need really good parallelism, squareness etc. on your truing stand to get away without one; it's a lot easier to knock one up out of a straight bit of board.- - - - - - - - - -
On Strava.{/url}0 -
Hub arrived this morning (3 days from ordering, so can't be faulted), new (to me) 360 degree vice acquired for nada yesterday to allow full unrestricted movement on building stand (can't really be called a truing stand), so all a go - go.
Wheel will be fully degreased today and rebuild research starts in earnest. Can't wait for some random reason.Postby team47b » Sun Jun 28, 2015 11:53 am
De Sisti wrote:
This is one of the silliest threads I've come across.
Recognition at last Matthew, well done!, a justified honoursmithy21 wrote:
He's right you know.0 -
Matthew,
Good to see everything coming together. That swivel vice will be a useful addition to the workshop, not just for the wheels. The lacing up of the wheels I found to be quite time consuming, checking everything was in the right order. I think that the most difficult part will be the spoke tension.As I have a good pair of wheels from CycleClinic I'll be using the sound/feel of those as my target, and I'll be trying a guitar tuner to see if that helps.
Anyway, thought I'd put a couple of pics up for anyone whose remotely interested.
http://imageshack.com/a/img829/1344/4xx9.jpg
http://imageshack.com/a/img819/1659/41jw.jpg
Desweller,
Thanks for the comments, it was your initial post about plywood that spurred me on to getting something knocked up as I've had the wheels laced up for over a month. The plan is to do the radial and lateral truing then dish them by just swopping the wheel over in the jig. Wheel see what happens.0 -
6wheels wrote:Matthew,
Good to see everything coming together. That swivel vice will be a useful addition to the workshop, not just for the wheels. The lacing up of the wheels I found to be quite time consuming, checking everything was in the right order. I think that the most difficult part will be the spoke tension.As I have a good pair of wheels from CycleClinic I'll be using the sound/feel of those as my target, and I'll be trying a guitar tuner to see if that helps.
Anyway, thought I'd put a couple of pics up for anyone whose remotely interested.
http://imageshack.com/a/img829/1344/4xx9.jpg
http://imageshack.com/a/img819/1659/41jw.jpg
Desweller,
Thanks for the comments, it was your initial post about plywood that spurred me on to getting something knocked up as I've had the wheels laced up for over a month. The plan is to do the radial and lateral truing then dish them by just swopping the wheel over in the jig. Wheel see what happens.
I see what you're saying. Looking at your stand, you'll need to be quite careful that your QR is always done up tight or your wheel will tilt and give you a mis-reading. You might find yourself wanting to add some triangulation in to support the weight of the wheel better. Is your truing gauge going to be screwed to the stand somehow?- - - - - - - - - -
On Strava.{/url}0