Electronic Suspension System
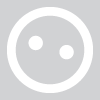
vkolotov
Posts: 15
Hi all, I just want to show you what I achieved by combining of my two hobbies: biking and micro-controllers.
So, you will find below a short report about «Electronic Suspension System» (ESS). I am not going to make a long introduction, let's see some photos and videos:


Video on youtube
So now let's get down to the details.
The problem:
As you may know, a lot of rider energy is wasted for dumping suspension/shocks while pedaling on the full suspension bike, this is very true for both suspension fork and rear shock. The rear suspension is almost always subject to the dumping, the front suspension is mainly exposed while pedaling "in standing position".
To solve this problem a lot of manufacturers invented various mechanical/hydraulics systems to prevent loosing your energy and gain more efficiency while pedaling. This includes: Fox ProPedal, RockShox MotionControl, e.t.c.
There is no doubt that these systems help you to improve efficiency. However they do not eliminate power dissipation completely, as these solutions are “passive”. In other words, mechanical/hydraulics systems do not take into account external factors like:
Therefore, in recent years major bike manufacturers developed "active" suspension control systems that take into consideration the above-mentioned external conditions through the various sensors:
The idea:
As it usually happens in my country, the problem was posed as follows: "To surpass these analogues in all possible characteristics, several times". Namely, these systems had to be caught up and overtaken in terms of:
What was achieved:
1. Efficiency
Firstly, in contrast to the systems which are developed by major manufacturers, this system controls both fork and rear suspensions simultaneously.
Secondly, the hardware (micro-controller) allows to implement any possible algorithm to control suspensions, by using general-purpose high-level programming language - C++.
2. Dimensions
Specially selected/developed components of the system are so small so that they can be placed directly inside of the steerer tube. I.e. the “brain” and rechargeable battery are fitted into the fork steerer so the dimensions of the controller are about 150mm х 19mm. As a result, in my opinion, this is an elegant solution, which is not even visible. And the most important thing is that nothing sticks out and does not take useful place, e.g. how it is done here (the bulky battery pack attached instead of a vital water bottle):

3. Weight
Everyone knows that weight is very crucial factor in biking. So, I tried hard to make it as much as possible lightweight. As a result, the weight of the system is about 120 gr. For the reference: the weight of the "E.I. Shock" system is 350 gr.
4. Intelligence
Sensors and ability to be programmed allows to implement any possible algorithm by using C++ programming language, the following were implemented so far:
Manual mode
This mode allows a rider to control lock-outs of the fork and rear suspensions by clicking on the one of the three buttons, which are located on the handle bar under the rubber handle. You may see how it works on the video above. Although this mode is simple, it is still very helpful and useful feature, since it is quite difficult to adjust settings of the shocks while you are pedaling.
Semi-automatic mode
Mostly, this mode was designed for the new type of the FOX shocks, which have CTD adjuster. The main idea of this mode is to leverage mechanics/hydraulics features of the shocks, i.e. the system in accordance with readings of the sensors chooses one of the three modes of the FOX shock, e.g “climb”, “trail” and “descend”, taking advantage of the shock hardware in order to optimize efficiency. The mode (CTD) of the shock is chosen by turning the servos to a particular angle.
Currently, CTD modes are selected based on the angle of inclination of the bike, in other words, this works as follows:
This mode was designed especially for the one of the respected rider, but at the last moment he changed his sponsor, and the installation on his brand new bike has become impossible.
Here you can see how it works on youtube.
Automatic mode
This is the most interesting and complex mode as it is intended maximally increase pedaling efficiency by switching on/off lockouts in very particular moments when it is really needed.
For the implementation of this mode, there were distinguished several possible states of the systems and transition rules between them, to cut a long story short this looks like as follows:
The system, by using the following sensors:
Calculates the following parameters:
Based on these parameters, the system chooses necessary state, by switching from one state to another:
System state (riding mode)
Suspensions state
Idle
All suspensions are locked
Pedaling while standing over the handle bar
All suspensions are locked
Pedaling
Fork is unlocked, rear shock is locked
Free rolling
All suspensions are unlocked
Absorbing
All suspensions are unlocked
Unfortunately, I have not made any video demonstrating this mode, hopefully when I get a GoPro camera I'll make a video.
But for now, here is a video of it in static on youtube
5. Possibility to pair with mobile devices
Through the internal bluetooth module it is possible to pair a mobile device with the system to display system telemetry and to adjust various system settings.
At the moment, an android application was created which can be used as ordinary “bike computer” and to edit system settings.
Here are some screen shots of it:
Manual mode:

CTD mode:

Red line - raw readings of the bike inclination
Blue line - bike inclination, obtained by applying a mathematical filter
Climb/Descend gradient threshold - threshold angles of the Climb/Trail/Descend modes (could be adjusted by moving slider or through the buttons on the handle bar). Also, these thresholds are shown on the chart as dotted lines
Automatic mode:

Red line - unsprung accelerometer sensor readings (on the fork lowers)
Blue line - sprung accelerometer sensor readings (inside the fork steerer)
Sprung/Unsprung severity thresholds - these are values are used to determine when fork and rear shock should be locked. When “Sprung” value is exceeded, the rear shock is locked. When “Unsprung” value is exceeded, the fork is locked, but only in case when “Sprung” value is not exceeded, i.e. when there are no bumps (these values can be adjusted by moving slider or through the buttons on the handle bar). Also, these thresholds are shown on the chart as dotted lines.
System settings adjustment:

The first two screen shots – calibration of the servos. When the sliders are being moved, the servos are moving too in real time, in accordance with sliders values (degrees). This is just a small part of available options, there are about 50 various settings.
Here are some videos:
Manual mode: First video Second video
CTD mode: on youtube
Servos calibration: on youtube
Of course, in the future it will be possible to adapt the android application for the iPhone and other devices with bluetooth (may be iPad?
).
Soon, I get this device with running android OS on it, after what I am going to adapt the android application for this watches. Seems to me, it can be very interesting and convenient:

5. Cheapness
All the components which are used in the system can be bought on ebay.com or dx.com for a very little price. But for this prototype I bought the same components but for higher price, since I didn't want to wait delivering. As a result I spent as follows:
ebay.com or dx.com
local stores
Microcontroller
$10
$50
Accelerometer sensors (x2)
~$10
~$60
Battery (18650)
$6
$16
Buttons module
~$2
~$4
Reed switches
no information
no information
Wires
~$3
$5
Servos (very robust, with metallic
gears and bearings, the fastest, x2)
$20
$43
Links/joints (RC modeling)
$2
$10
Bluetooth board
$8
~$18
Solid State Relays, Li-Ion batteries
charger (microchip), other stuff
~$10
~$22
In total:
~$72
~$240
I have no idea how much factory-built system will cost, seems to me much more expensive.
6. Availability
All the components can be found at local stores, but for higher price. If you can wait delivering, you can buy them on ebay.com or dx.com. Also, I doubt that factory-built systems will be available even in 2013 (at least at my local stores where I live).
7. Ease of installation on existing equipment with minimal modifications
There were drilled only one hole in the fork plastic adjuster and only one hole in the rear shock adjuster. Then, links were screwed to these holes and joined to servos. The links are basic RC parts (they are used in some ordinary RC helicopter or plane). The servos are mounted on the plastic strip through the plastic and rubber mounts that I found at my home (mostly they were taken from old bike computers). As a results, seems to me, it is quite possible to install this system to any similar bike.
8. Maintainability
As you can see, the system consists of a set of components/modules, each of which is easily accessible and replaceable. You can imagine what will happen if the factory-built shock is broken, most likely it is impossible to fix it. The same is true for bottom bracket, where the manufacturer managed to place cadence sensor, seems to me you will throw out this BB in case of damage.
9. Fault tolerance
Even if the battery ran down or wires suddenly were cut off or fire occurred on your bike, it would be possible to adjust fork and rear suspension by hand. Most probably, factory-built suspensions (AFAIK) will be jammed. The servos are treated with special rubber compound for waterproofing.
10. Hardware upgrade
The system was designed in accordance with modular approach. At the moment, there is still opportunity to extend (free connectors) the system with additional sensors (HRM sensor) and other devices (e.g. LCD screen for displaying speed, cadence, distance and other bike computer functions).
11. Software upgrade
At any time, the microcontroller can be flushed with new version of the firmware via USB. You may imagine how it's great when you can realize any whim.
In future plans I have the following to implement:
Sleep mode
During downtime the system consumes only 1mAh. This is due to three solid-state relays, which cut off the servos, bluetooth and port i2c (for LCD screen, but currently unused). Therefore, I may predict that the system can wait for months in inactive state (it only depends on the internal resistance of the battery, i.e. how long the battery can hold its charge without load). The sleep mode is activated by timeout (timeout can be adjusted). The system wakes up after receiving an event of a button on the handle bar or by an event of the cadence sensor.
Active mode
Again, due to solid-state relays all servos are disconnected right after their use. Therefore, about 80% of the time the servos are not connected to the electric circuit, which leads to dramatic battery energy savings. Apart of that, bluetooth module can be disconnected from circuit by activating independent relay, so operation time can be increased when bluetooth is turned off. The bluetooth module can be switched off through the buttons on the handle bar or by timeout (can be adjusted).
Current consumption
Length of life on a single charge (estimated)
Sleep mode
1mA
4 months (without taking into account internal resistance of the battery)
Active mode
20mA
6 days (continuous running)
Active mode + bluetooth
40mA
2.5 days (continuous running)
Active mode + servos
150mA
20 hours (continuous running, i.e. if servos were used nonstop)
13. Charging the system through any USB port
Due to internal charging microchip the system can charge itself via any USB port. Time to full charge is about 10 hours. Charging is automatically turned off when the battery is fully charged, thus prevents "overcharge" of the battery, therefor overall battery life is increased.
Conclusion
The system has been developed for several month. At the moment, it is still being developed. Unfortunately, bike season ended and probably it would be difficult to continue testing it for now. But even now, I have strong feeling that the system really help you to increase pedaling efficiency.
Your comments are welcome.
So, you will find below a short report about «Electronic Suspension System» (ESS). I am not going to make a long introduction, let's see some photos and videos:


Video on youtube
So now let's get down to the details.
The problem:
As you may know, a lot of rider energy is wasted for dumping suspension/shocks while pedaling on the full suspension bike, this is very true for both suspension fork and rear shock. The rear suspension is almost always subject to the dumping, the front suspension is mainly exposed while pedaling "in standing position".
To solve this problem a lot of manufacturers invented various mechanical/hydraulics systems to prevent loosing your energy and gain more efficiency while pedaling. This includes: Fox ProPedal, RockShox MotionControl, e.t.c.
There is no doubt that these systems help you to improve efficiency. However they do not eliminate power dissipation completely, as these solutions are “passive”. In other words, mechanical/hydraulics systems do not take into account external factors like:
- Speed
- Cadence
- Type of terrain
Therefore, in recent years major bike manufacturers developed "active" suspension control systems that take into consideration the above-mentioned external conditions through the various sensors:
- Speed and cadence sensors
- Accelerometers sensors
The idea:
As it usually happens in my country, the problem was posed as follows: "To surpass these analogues in all possible characteristics, several times". Namely, these systems had to be caught up and overtaken in terms of:
- Efficiency
- Dimensions
- Weight
- Possibility to pair with mobile devices
- Intelligence
- Cheapness
- Availability
- Ease of installation on the existing equipment (fork and rear shock) with minimal modifications
- Maintainability
- Fault tolerance
- Hardware upgrade
- Software upgrade
- Low power consumption
What was achieved:
1. Efficiency
Firstly, in contrast to the systems which are developed by major manufacturers, this system controls both fork and rear suspensions simultaneously.
Secondly, the hardware (micro-controller) allows to implement any possible algorithm to control suspensions, by using general-purpose high-level programming language - C++.
2. Dimensions
Specially selected/developed components of the system are so small so that they can be placed directly inside of the steerer tube. I.e. the “brain” and rechargeable battery are fitted into the fork steerer so the dimensions of the controller are about 150mm х 19mm. As a result, in my opinion, this is an elegant solution, which is not even visible. And the most important thing is that nothing sticks out and does not take useful place, e.g. how it is done here (the bulky battery pack attached instead of a vital water bottle):

3. Weight
Everyone knows that weight is very crucial factor in biking. So, I tried hard to make it as much as possible lightweight. As a result, the weight of the system is about 120 gr. For the reference: the weight of the "E.I. Shock" system is 350 gr.
4. Intelligence
Sensors and ability to be programmed allows to implement any possible algorithm by using C++ programming language, the following were implemented so far:
Manual mode
This mode allows a rider to control lock-outs of the fork and rear suspensions by clicking on the one of the three buttons, which are located on the handle bar under the rubber handle. You may see how it works on the video above. Although this mode is simple, it is still very helpful and useful feature, since it is quite difficult to adjust settings of the shocks while you are pedaling.
Semi-automatic mode
Mostly, this mode was designed for the new type of the FOX shocks, which have CTD adjuster. The main idea of this mode is to leverage mechanics/hydraulics features of the shocks, i.e. the system in accordance with readings of the sensors chooses one of the three modes of the FOX shock, e.g “climb”, “trail” and “descend”, taking advantage of the shock hardware in order to optimize efficiency. The mode (CTD) of the shock is chosen by turning the servos to a particular angle.
Currently, CTD modes are selected based on the angle of inclination of the bike, in other words, this works as follows:
- Bike goes uphill – the servo chooses Climb mode
- Bike goes straight - Trail mode is switched on
- Bike goes downhill - Descent mode
This mode was designed especially for the one of the respected rider, but at the last moment he changed his sponsor, and the installation on his brand new bike has become impossible.
Here you can see how it works on youtube.
Automatic mode
This is the most interesting and complex mode as it is intended maximally increase pedaling efficiency by switching on/off lockouts in very particular moments when it is really needed.
For the implementation of this mode, there were distinguished several possible states of the systems and transition rules between them, to cut a long story short this looks like as follows:
The system, by using the following sensors:
- Accelerometer sensor (sprung sensor, inside of the steerer)
- Accelerometer sensor (unsprung sensor, on the fork lowers)
- Speed sensor
- Cadence sensor
Calculates the following parameters:
- Severity of the impact (bump severity)
- Movement of the fork in the vertical plane and in the plane perpendicular to the bike movement (headway movement)
- Angle of the bike inclination
- Speed
- Cadence
Based on these parameters, the system chooses necessary state, by switching from one state to another:
System state (riding mode)
Suspensions state
Idle
All suspensions are locked
Pedaling while standing over the handle bar
All suspensions are locked
Pedaling
Fork is unlocked, rear shock is locked
Free rolling
All suspensions are unlocked
Absorbing
All suspensions are unlocked
Unfortunately, I have not made any video demonstrating this mode, hopefully when I get a GoPro camera I'll make a video.
But for now, here is a video of it in static on youtube
5. Possibility to pair with mobile devices
Through the internal bluetooth module it is possible to pair a mobile device with the system to display system telemetry and to adjust various system settings.
At the moment, an android application was created which can be used as ordinary “bike computer” and to edit system settings.
Here are some screen shots of it:
Manual mode:

CTD mode:

Red line - raw readings of the bike inclination
Blue line - bike inclination, obtained by applying a mathematical filter
Climb/Descend gradient threshold - threshold angles of the Climb/Trail/Descend modes (could be adjusted by moving slider or through the buttons on the handle bar). Also, these thresholds are shown on the chart as dotted lines
Automatic mode:

Red line - unsprung accelerometer sensor readings (on the fork lowers)
Blue line - sprung accelerometer sensor readings (inside the fork steerer)
Sprung/Unsprung severity thresholds - these are values are used to determine when fork and rear shock should be locked. When “Sprung” value is exceeded, the rear shock is locked. When “Unsprung” value is exceeded, the fork is locked, but only in case when “Sprung” value is not exceeded, i.e. when there are no bumps (these values can be adjusted by moving slider or through the buttons on the handle bar). Also, these thresholds are shown on the chart as dotted lines.
System settings adjustment:

The first two screen shots – calibration of the servos. When the sliders are being moved, the servos are moving too in real time, in accordance with sliders values (degrees). This is just a small part of available options, there are about 50 various settings.
Here are some videos:
Manual mode: First video Second video
CTD mode: on youtube
Servos calibration: on youtube
Of course, in the future it will be possible to adapt the android application for the iPhone and other devices with bluetooth (may be iPad?

Soon, I get this device with running android OS on it, after what I am going to adapt the android application for this watches. Seems to me, it can be very interesting and convenient:

5. Cheapness
All the components which are used in the system can be bought on ebay.com or dx.com for a very little price. But for this prototype I bought the same components but for higher price, since I didn't want to wait delivering. As a result I spent as follows:
ebay.com or dx.com
local stores
Microcontroller
$10
$50
Accelerometer sensors (x2)
~$10
~$60
Battery (18650)
$6
$16
Buttons module
~$2
~$4
Reed switches
no information
no information
Wires
~$3
$5
Servos (very robust, with metallic
gears and bearings, the fastest, x2)
$20
$43
Links/joints (RC modeling)
$2
$10
Bluetooth board
$8
~$18
Solid State Relays, Li-Ion batteries
charger (microchip), other stuff
~$10
~$22
In total:
~$72
~$240
I have no idea how much factory-built system will cost, seems to me much more expensive.
6. Availability
All the components can be found at local stores, but for higher price. If you can wait delivering, you can buy them on ebay.com or dx.com. Also, I doubt that factory-built systems will be available even in 2013 (at least at my local stores where I live).
7. Ease of installation on existing equipment with minimal modifications
There were drilled only one hole in the fork plastic adjuster and only one hole in the rear shock adjuster. Then, links were screwed to these holes and joined to servos. The links are basic RC parts (they are used in some ordinary RC helicopter or plane). The servos are mounted on the plastic strip through the plastic and rubber mounts that I found at my home (mostly they were taken from old bike computers). As a results, seems to me, it is quite possible to install this system to any similar bike.
8. Maintainability
As you can see, the system consists of a set of components/modules, each of which is easily accessible and replaceable. You can imagine what will happen if the factory-built shock is broken, most likely it is impossible to fix it. The same is true for bottom bracket, where the manufacturer managed to place cadence sensor, seems to me you will throw out this BB in case of damage.
9. Fault tolerance
Even if the battery ran down or wires suddenly were cut off or fire occurred on your bike, it would be possible to adjust fork and rear suspension by hand. Most probably, factory-built suspensions (AFAIK) will be jammed. The servos are treated with special rubber compound for waterproofing.
10. Hardware upgrade
The system was designed in accordance with modular approach. At the moment, there is still opportunity to extend (free connectors) the system with additional sensors (HRM sensor) and other devices (e.g. LCD screen for displaying speed, cadence, distance and other bike computer functions).
11. Software upgrade
At any time, the microcontroller can be flushed with new version of the firmware via USB. You may imagine how it's great when you can realize any whim.
In future plans I have the following to implement:
- All possible function of the bike computer (including those which are available only on the top-level bike computers).
- Deeper analysis of the road surface (asphalt, tree roots, rocks e.t.c) in order to determine some internal factors more precisely.
- A lot more functions (even a bike alarm/security system)...
Sleep mode
During downtime the system consumes only 1mAh. This is due to three solid-state relays, which cut off the servos, bluetooth and port i2c (for LCD screen, but currently unused). Therefore, I may predict that the system can wait for months in inactive state (it only depends on the internal resistance of the battery, i.e. how long the battery can hold its charge without load). The sleep mode is activated by timeout (timeout can be adjusted). The system wakes up after receiving an event of a button on the handle bar or by an event of the cadence sensor.
Active mode
Again, due to solid-state relays all servos are disconnected right after their use. Therefore, about 80% of the time the servos are not connected to the electric circuit, which leads to dramatic battery energy savings. Apart of that, bluetooth module can be disconnected from circuit by activating independent relay, so operation time can be increased when bluetooth is turned off. The bluetooth module can be switched off through the buttons on the handle bar or by timeout (can be adjusted).
Current consumption
Length of life on a single charge (estimated)
Sleep mode
1mA
4 months (without taking into account internal resistance of the battery)
Active mode
20mA
6 days (continuous running)
Active mode + bluetooth
40mA
2.5 days (continuous running)
Active mode + servos
150mA
20 hours (continuous running, i.e. if servos were used nonstop)
13. Charging the system through any USB port
Due to internal charging microchip the system can charge itself via any USB port. Time to full charge is about 10 hours. Charging is automatically turned off when the battery is fully charged, thus prevents "overcharge" of the battery, therefor overall battery life is increased.
Conclusion
The system has been developed for several month. At the moment, it is still being developed. Unfortunately, bike season ended and probably it would be difficult to continue testing it for now. But even now, I have strong feeling that the system really help you to increase pedaling efficiency.
Your comments are welcome.
0
Comments
-
Nice.0
-
Bonkers. I got lost after the pictures but looks great. All credit it to you for working it through..0
-
I'm not sure whether to say wow or seriously?
Way too complex for me personally, and 99% of riders I suspect.
Especially considering some of the questions we get on here.I don't do smileys.
There is no secret ingredient - Kung Fu Panda
London Calling on Facebook
Parktools0 -
What!? There's a risk of fire!?
Many of us ride to get away from technology. Digitising cycling is going to upset many people, even if it's only doing what mechanical designs are currently doing, but faster and more efficiently. Congratulations on what looks to be an awesome design adventure, but this doesn't excite me.0 -
Wow, good effort. I can see how that would appeal to some riders.0
-
That's a great effort, whether or not you want it is something else, but that's mental!0
-
Fiving up a lot with this post. Why not build and market it?0
-
bluechair84 wrote:What!? There's a risk of fire!?.
Gotta say, that was one thing that jumped out at me too. I think (hope) it is just something lost in translation.
It does rather seem like a solution looking for a problem if I'm perfectly honest though.
Another thing that jumps out at me is that you don't appear to mention weatherproofing. All those servos and stuff, my main concern would be sealing from the elements, especially round here where it's always wet, and there is a lot of salt in the air/mud. Apologies if you did mention it and I just missed it.
And kudos to you for taking something like this on, I'd not even have a clue where to start with it.0 -
Good work there, I can't remember what mag It was in a couple of months ago but I was reading a article about this. I like the idea of it but I can't stop wondering if our bikes are starting to get to complicated and its just one more thing that can go wrong while out on the trailsIt's not a ornament, so ride It0
-
boristhespie wrote:Fiving up a lot with this post. Why not build and market it?
Im sure I read somewhere (might have been MBR) that Lapierre were doing exactly this...0 -
vkolotov wrote:4. Intelligence
Sensors and ability to be programmed allows to implement any possible algorithm by using C++ programming language, the following were implemented so far:
...
I haven't read the whole thing (sorry!) but what comes to mind is the chance of the system getting it wrong. Say I'm rattling along and the system suddenly decides I'm climbing and locks out the shocks as I hit something big? If I wipe out in a big way I don't want to have to blame some shoddy logic. (I'm a software dev. Bad logic happens :roll: )0 -
cyd190468 wrote:You may have trouble convincing people that the complexity is justified when you can have a bar mounted cable remote that does basically the same thing. Like on my new Scott that I pick up on friday
The selling point is that it's live and active, and takes real time data from what you are doing on the bike to constantly adjust how the bike behaves. Like 4x4 systems in cars, by monitoring everything electronically it can provide more power where the grip is rather than just dumbly driving everything or nothing.
Is our riding terrain really so complex as to need increasingly more frequent changes in suspension, or is it so complicated as to utterly overwhelm an 'intelligent' system? Afterall I can see this is being a really problem with no obvious solution;Pedaling while standing over the handle bar
All suspensions are locked0 -
bluechair84 wrote:What!? There's a risk of fire!?
Many of us ride to get away from technology. Digitising cycling is going to upset many people, even if it's only doing what mechanical designs are currently doing, but faster and more efficiently. Congratulations on what looks to be an awesome design adventure, but this doesn't excite me.
I'm here and going to answer all the questions.
Well, fire - actually, it was very stupid joke, which, seems to me, nobody understand. Sorry for that.0 -
You may have trouble convincing people that the complexity is justified when you can have a bar mounted cable remote that does basically the same thing. Like on my new Scott that I pick up on friday
It doesn't though does it, not even close.0 -
Cat With No Tail wrote:bluechair84 wrote:What!? There's a risk of fire!?.
Gotta say, that was one thing that jumped out at me too. I think (hope) it is just something lost in translation.
It does rather seem like a solution looking for a problem if I'm perfectly honest though.
Another thing that jumps out at me is that you don't appear to mention weatherproofing. All those servos and stuff, my main concern would be sealing from the elements, especially round here where it's always wet, and there is a lot of salt in the air/mud. Apologies if you did mention it and I just missed it.
And kudos to you for taking something like this on, I'd not even have a clue where to start with it.
Again, fire is stupid joke. There is no any risk of fire.
About waterproofing. Yeap, sure, I thought about this, and covered the servos with special rubber compound. To be mor eprecise, I treated them with PlastiDip.0 -
njee20 wrote:You may have trouble convincing people that the complexity is justified when you can have a bar mounted cable remote that does basically the same thing. Like on my new Scott that I pick up on friday
It doesn't though does it, not even close.
That is right, it does a lot more than basic mechanical remote lock-outs.0 -
Sarnian wrote:Good work there, I can't remember what mag It was in a couple of months ago but I was reading a article about this. I like the idea of it but I can't stop wondering if our bikes are starting to get to complicated and its just one more thing that can go wrong while out on the trails
Thank you.
Actually, I mentioned that there are analogues systems are being developed by major manufacturers.
Like that. Apart of that, there are other electronic systems built by Specialized (I've just heard about it, not sure that they gonna forget their "brain" suspention), Cannondale. But all these systems control only rear OR fork suspensions, and they cannot be paired with mobile devices (actually, I tried to enumerate all possible plus points of my system in comparison to analogues at this article).0 -
craker wrote:vkolotov wrote:4. Intelligence
Sensors and ability to be programmed allows to implement any possible algorithm by using C++ programming language, the following were implemented so far:
...
I haven't read the whole thing (sorry!) but what comes to mind is the chance of the system getting it wrong. Say I'm rattling along and the system suddenly decides I'm climbing and locks out the shocks as I hit something big? If I wipe out in a big way I don't want to have to blame some shoddy logic. (I'm a software dev. Bad logic happens :roll: )
Never mind, it is really very long article.
Sure, there are always bugs in any software. I tried hard to get rid of all bugs, and still doing it. So, all the major bugs, seems to me, were eliminated. There are about ~3000 lines of code written in C++. It is not so many comparing to enterprise applications, but we should bear in mind that this code is for embeded systems, so it has to be more compact.0 -
bluechair84 wrote:Pedaling while standing over the handle bar
All suspensions are locked
Well, the logic is more complex than you think. The suspensions would not be locked if there were bumps on the trail.
That is why, the system employs accelerometer sensors in order to determine bumps on the road.0 -
Well done mate big high five to you. I briefly thought about doing something similar my self when I heard about the Rockshox system. But I realised I didn't personally need or want such a thing so wasn't sure I'd have the motivation to make it happen. The manufacturers clearly think there is a market for it hence developing these systems.
Best of luck to you.0 -
somebody give this man a job, quick0
-
Some nice ideas & if it works and was developed to a production model I would buy this over the Fox CTD system as it allows better control over the suspension set up where the fox system seriously limits your set up.Transition Patrol - viewtopic.php?f=10017&t=130702350
-
Slightly different animals I think.I don't do smileys.
There is no secret ingredient - Kung Fu Panda
London Calling on Facebook
Parktools0 -
vkolotov wrote:bluechair84 wrote:Pedaling while standing over the handle bar
All suspensions are locked
Well, the logic is more complex than you think. The suspensions would not be locked if there were bumps on the trail.
That is why, the system employs accelerometer sensors in order to determine bumps on the road.
I'm sure with a lot of time and effort you could use the sensors to determine very specific scenarios and have the system respond appropriatly, I think we're all impressed that this is what you're aiming to achieve. One of the reasons why I wouldn't be keen is that I like to be able to fix evrything myself. Such as system is one more thing to look after and probably requires tools and skills I don't have to keep sweet. Bikes are becoming more and more complex, I think there will always be a place for 'dumb' systems so long as they are efficient. But either way, I think it's commendable what you're achieving.
Thinking about it... the electronics in my house and my car are far more reliable than the analogue things... maybe I really am a ludite :shock:0 -
bluechair84 wrote:vkolotov wrote:bluechair84 wrote:Pedaling while standing over the handle bar
All suspensions are locked
Well, the logic is more complex than you think. The suspensions would not be locked if there were bumps on the trail.
That is why, the system employs accelerometer sensors in order to determine bumps on the road.
I'm sure with a lot of time and effort you could use the sensors to determine very specific scenarios and have the system respond appropriatly, I think we're all impressed that this is what you're aiming to achieve. One of the reasons why I wouldn't be keen is that I like to be able to fix evrything myself. Such as system is one more thing to look after and probably requires tools and skills I don't have to keep sweet. Bikes are becoming more and more complex, I think there will always be a place for 'dumb' systems so long as they are efficient. But either way, I think it's commendable what you're achieving.
Thinking about it... the electronics in my house and my car are far more reliable than the analogue things... maybe I really am a ludite :shock:
I see your point. Everything in our world inevitably develops/evolves. And it is so cool, when you are riding your bike and your bike lives his life by switching suspensions automatically without your participation, thereby helps you to make your ride more efficient.0 -
On the one hand, you have people like yourselves that want to see technology used to its greatest capacity, 'it can be done, therefore why not try?'. And on the other you have people who shun such advances as it is diluting the experience of riding. The idea that your bike is a 'co-pilot' (by your analogy) that assists your riding is really against what I want out of the experience as I like to feel that I made it up and down 'that' without the aids of someone in a lab somewhere turning my energies in logic sequences and programming responses from a system. It can be put on a bi-polar scale:
Full technical advantage <
> no technical advantage.
But of course, I wouldn't want to omit my damper cartridges, or my indexed mechs, or selectable gear ratios, or butted tubes, or alloys... I'm sure we're all hypocrites in this sense, we don't want technology invading the victories that we see as ours, even though it already has. But a computer system I see as one step too far. And I mean no disrespect to what you've produced - it really is fantastic and there will be people out there who want the advantage, but I'm not ready for it yet.0 -
Hey, hi all! I'm on bikerumor!
On the main page.
http://www.bikerumor.com/2012/11/26/hac ... e-buttons/0 -
Although yours maybe cheap, it is also available on a Ghost; the E:i has fork sensors, bottom bracket sensors, computer, display and automatic shock adjustment (I don't think it has auto fork adjust). I just came across an advert for it in Dirt and thought of this thread.0
-
bluechair84 wrote:Although yours maybe cheap, it is also available on a Ghost; the E:i has fork sensors, bottom bracket sensors, computer, display and automatic shock adjustment (I don't think it has auto fork adjust). I just came across an advert for it in Dirt and thought of this thread.
Actually, I mentioned this in the my article0 -
vkolotov wrote:bluechair84 wrote:Although yours maybe cheap, it is also available on a Ghost; the E:i has fork sensors, bottom bracket sensors, computer, display and automatic shock adjustment (I don't think it has auto fork adjust). I just came across an advert for it in Dirt and thought of this thread.
Actually, I mentioned this in the my article0