Help a team of mechanical engineering students reinvent the modern drivetrain!
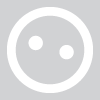
We are a group of French Canadian mechanical engineering students who, for their final engineering project, decided to figure out a way to solve some of the major issues found on modern bicycle drivetrains. We have a year and a half to develop and build a functioning prototype of a drivetrain that solves two major problems: The inability of current drivetrains to safely shift under load and/or the incredible vulnerability of modern derailleurs.
Current derailleur systems have been around for the last 150 years, and they do their job well. Altough, those 150 years of refinement blinds us of the fact that they are incredibly fragile, exposed to the elements, vulnerable to impacts and won't shift properly when load is applied (aka when you actually need to shift). It is safe to say that a lot of people around here have had their fair share of frustration due to their drivetrains. Either getting their day ruined by a bent or broken derailleur hanger/cage, or even the countless hours we spend trying to adjust the damn things. When we think about it, isn't it absurd that after 150 years, we still hang our 600$ transmission under the back wheel, waiting to be knocked off or bent by a root, rock or even ourselves trying to shift down a couple gears to get up that sudden steep section?
So here we are, in front of a blank white board. We have researched a fair bit on various alternative solutions such as gearboxes (Pinion is a good example), CVTs, hubs, or simply relocating the derailleur to a less exposed location. We want to hear your opinion on the matter. Any kind of feedback is valuable. You have complaints about current drivetrains? Great, lets hear it. You have experience with gearboxes and/or other types of bicycle drivetrains? Great! Lets hear it! You have ideas, suggestions, or even want to roast us for trying to solve problems that you think don't exist? Go ahead! We want all the feedback we can get!
We are also aware that trying to solve every problems at the same time is the best way to create something that won't work/solve anything. We are trying to narrow down our list of problems to identify which problems need to be solved the most and which angle of approach we should take. So please help us begin our journey and leave a comment below!
Cheers!
Comments
-
There are different markets that will love or hate your solution for different reasons.
If you produce something that is clean, maintenance free and is easy to use, you will get plaudits from commuters, beginners, people who are not "handy" and technophobes. But the keen rider and onwards to professionals will hate the fact that it is too heavy, can't be tinkered with, or tuned; but mostly because it will be too heavy. Both will hate you because it costs more to buy (they won't care about the reduced maintenance costs).
But the electric bike market mostly don't care about weight, after all they have accepted the additional 7-8kg that the average emtb weighs more than the analogue bike they used to ride before.
To an extent they also don't care about cost because a emtb will cost between £1200 - £1500 more than the analogue bike they had before that was similarly equipped to ride where they like to ride. The other thing to take into account is who is riding the emtbs. My view based upon who I meet and who I know is that the average age is considerably older than the average for most mtbs. This could be because (like me) there is some type of infirmity that has been restricting the type of terrain and/or the distance travelled, frequency of riding etc. Having some pedal assistance is the breakthrough that I and others want/need. Typically with age comes a bit more cash (no kids at hme, mortgage paid off etc)
What they do care about is something that will take the extra power going through the drive train and last as long as their analogue bike kit used to last. Chains, gears, jockey wheels all seem to wear out much more rapidly than they do on an analogue bike. Personally, I don't see that but on the emtb forum I'm also on it is a constant complaint. I believe it's caused by lack of mechanical sympathy when shifting gear (and many agree), but who knows? So maybe something that shifts gears better or maybe seamlessly like a variable speed gearbox can do.
EMTBs also have a motor that has gears in it. All the effort appears to be going into making them lighter (magnesium casing anybody). It wouldn't take much effort to insert a sun and planet type drive in there to give you two choices of output speed, with maybe a 5 speed VS drive in the rear hub to give you 10 gears that don't overlap. Yes I know that some emtbs have a 1x12 gear drive fitted, but trust me on this anyone other than those that have to have the latest bling do not want a 12-speed drive on an emtb. On a human powered analogue bike yes, on pedal assisted ebike, deffo not. The premium drive on ebikes is, would you believe, 8-speed. Wider and stronger chain, thicker and stronger gears. Made to last longer, simpler etc. But in practice, 8-speeds don't give enough steps and I'm always hunting for the right gear. In addition, the parts are very expensive. Riders with the premium EX1 (8-speed) kit are changing to 10-speed because you can buy three lots of 10-speed kit for the price of one lot of 8-speed EX1. Oh and by the way, whatever number of speeds you have it is the gear range that is important; all emtbs so far are 1x and the range is dictated by the cassette. So if you have an average 15% gap between gears, then the wider the range the better. So not 8 or 12, what about ten? Seems to be the happy medium, lots of emtb riders are opting for that. You have been able to get wide range 10-speed cassettes for a number of years now.
How about a belt drive? They are light, amazingly strong and robust. Hey, you could have that sexiest of material in there, carbon fibre! Or maybe even kevlar, graphene, or shock horror, unobtainium! But belt drives have been around since God was a boy and I would believe that the technology you need is already out there.
At last, I'm getting close to the end!
My recommendation would be to segment and analyse the market and aim for one type only. If it ends up suiting more than one you're onto a winner. I doubt very much if you will produce one solution that will suit all bikes and/or type of customer. There are many types of bikes from several hundred ££ to well over £10k. The type of bike varies from commuter to downhill via XC, Trail, Enduro (and others sure to come). You can also fit a motor and battery to pretty much any bike, but in my opinion few have the features that your project may be applied to with success.
For background knowledge and to check what I'm saying, take a look at the emtb websites below:
This one is great, is global in scope, and is very popular: https://www.emtbforums.com/
This one is also good, but more Euro-centric, not quite the same scope, but a good comparison: https://ebike-mtb.com/en/
PS: ebikes are where all the money is going in the industry and from the customers, check out the statistics. (No, I'm not going to do all the work for you" ) Check out how many ebikes, market share, and how fast it is growing.1 -
Is the goal to "not be a derailleur"? I know you've said "improve, resolve shortcomings etc" but such language often just means "well it's not that other thing, so yeah, better"
You could look at redesigning hub gears - I'd be a fan of producing something like the modern multispeed hubs (proven internals, sufficient gear range, less damage prone than derailleur systems) but engineer them to be part of the crank/BB assembly, simplifying wheels as they'd only have to carry a 1x1 final drive from the gearbox. As the final drive is coming from the gearbox not the cranks, you don't need to do that with a chain and sprockets (although that might be lightest and least threatening to a pretty conservative bicycle market).
If you're going to review and include the notion of using a derailleur as the shifting mechanism but in a new way, there's all manner of ways you could look at tooth/chain design, clutches, placement of the system relative to the cranks (some sort of mini derailleur setup running inside a frame triangle with a final drive to the wheel?)
Good, luck with your project, and yes, the key thing would be shifting under load, and vulnerability to damage, followed by weight and complexity (and cost)
There's always someone having a worse day than you.
Usually it's me.0 -
As a mountain bike rider and going off topic a little I would love it if there was a material that could be utilized that would make and an 'everlasting' chain and cassette cogs and all the things that wear down over the space of a year or two.
Would making these parts out of exotic materials such as Tungten Carbide (WC) be viable? I've heard it's tougher than dried on Weetabix?
Is it a plausible material that could be manufactured to suit chain and cogs? If it could to be used what would be the cost to end customer, is it financially within reach to produce using this or maybe a similar material? There could be a downside that makes it not suitable besides financial and manufacturing reasons, I wouldn't know but in layman's terms it sounds like the ideal material to me.0 -
At a guess it's simply cost. There's no reason the components on a bike drive train couldn't be manufactured out of exotic alloys much stronger than steel which would have longer service lives.reaperactual48 said:As a mountain bike rider and going off topic a little I would love it if there was a material that could be utilized that would make and an 'everlasting' chain and cassette cogs and all the things that wear down over the space of a year or two.
Would making these parts out of exotic materials such as Tungten Carbide (WC) be viable? I've heard it's tougher than dried on Weetabix?
Is it a plausible material that could be manufactured to suit chain and cogs? If it could to be used what would be the cost to end customer, is it financially within reach to produce using this or maybe a similar material? There could be a downside that makes it not suitable besides financial and manufacturing reasons, I wouldn't know but in layman's terms it sounds like the ideal material to me.There's always someone having a worse day than you.
Usually it's me.1 -
Start by looking at patents for Sturmey Archer hub gears and Shimano Alfine. I'd second the thought of building it into the bottom bracket, so an internal gearbox. Done before and complex. You'd then be looking at frame design too. That's where you get into the constraints of the drivetrain being part of a system (the bicycle). You either work to some common standard for that (like hub widths, bottom bracket dimensions, chainset as part of final drive that may determine chain size/pitch) and compromise your design, or you need to go outside your intended scope.1
-
Tungsten Carbide is indeed tough and very, very, hard. It is so tough and hard that it is used as the cutting edges on machine tools (that bit at the end of your masonry drill will be TC). But it is heavy and very stiff. But your gears will last for ever! But even proper gearboxes (like in cars) don't use TC, so that should tell you something.reaperactual48 said:...............
Would making these parts out of exotic materials such as Tungten Carbide (WC) be viable? I've heard it's tougher than dried on Weetabix?
...........
The new wonder material for bikes is no longer carbon fibre, but Graphene. Graphene has so many superlatives it is pointless me picking out a few here, just Google it. It is so new that people don't even know what to do with it yet. It is definitely a solution looking for a problem. Imagine the frame, wheels, tyres, spokes, bars, grips, cables, hoses, levers, calipers, fork and shock (not sure about the drive train, hubs, bearings, discs & brake pads) all weighing just a few kilos!1 -
OOOHH my!
Is it a guy thing or just me that words like titanium, Tungsten carbide, carbon fibre and graphene makes my mouth water!
I'm no weight weenie and if I had a drivetrain made out of some of these materials that would 'last forever' would I buy it, yes but not if it costs more than the bike!1 -
Thank you all for your replies! We'll take a deeper look all those technologies you mentionned! I'll make sure to post updates of the project on here as the months go by!0
-
You can already get 14sp hub gears, bottom bracket gearboxes and Kevlar belt drive.
It’s just we like derailleurs because I’m almost 100% of cases the mech hangar breaks(as designed) not the mech and they cost pence to replace
I think you’re over egging the problem in my opinionGiant TCR Composite 1, Giant Defy Advanced 2, Boardman Comp, Santa Cruz Heckler, Raleigh M-Trax Ti, Strida LT, Giant Halfway0 -
https://www.youtube.com/watch?v=rgo-yEaXDzA
If you really want to overegg it...0 -
The would need the materials to be made from unobtanium to survive the power transmitted from a reasonably fit adult. The material not only needs to be strong and incredibly stiff, but hard wearing too. All those tiny ball races open to the elements mean that for the time being this is an indoor solution. And how strongly are they mounted? That is where the main failure will come from.
It is easy to criticise something new, but I can't be as jaw droppingly amazed as the guy in the video. If the tiny ball bearings were teeth, it would be a "Ho Hum yawn" from me, but the use of ball bearings strikes me as new.0