spoke tension
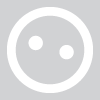
Clockworkmark31
Posts: 1,053
Hey all,
Quick question about spoke tension. Started hearing my front wheel creaking the more I leaned forward or cornering etc. Figured the spokes nipples need tweaking (adjusting) after the wheels not being touched since new. Went and bought the park tools gadget thing. And tightened the nipples one full turn, seems to have eliminated the creaking 95% but just how tight is too much?
Quick question about spoke tension. Started hearing my front wheel creaking the more I leaned forward or cornering etc. Figured the spokes nipples need tweaking (adjusting) after the wheels not being touched since new. Went and bought the park tools gadget thing. And tightened the nipples one full turn, seems to have eliminated the creaking 95% but just how tight is too much?
0
Comments
-
Depends on the build. I have some that twang like a guitar, some that feel quite loose. As as long as the tension is even and the wheel is true.I don't do smileys.
There is no secret ingredient - Kung Fu Panda
London Calling on Facebook
Parktools0 -
They need to be the correct tension. A tension gauge is useful .Transition Patrol - viewtopic.php?f=10017&t=130702350
-
Wheel looks quite true and was trying to do it without the tension gauge. They are just the standard wheelset that came with the bike until I can afford some Mavic ones.
Rims Giant S-XC2 27.5 wheelset
Hubs Giant Tracker Sport
Spokes Stainless Steel
Tyres Schwalbe Rapid Rob, 27.5x2.25"0 -
Thinking about it, even if I did have a tension gauge that I don't. How would I know what the correct tension should be?0
-
There are various guides on the Internet. Just google it.Transition Patrol - viewtopic.php?f=10017&t=130702350
-
One tip I had for wheel building without a spoke tension meter is to ping each spoke and make sure it produces the same tone. If your back wheel is the same build as your front that's probably a decent guide.0
-
Just read through this http://www.wheelpro.co.uk/support/tensiometers/ and it was an interesting read, but without suppliers stating (I know some do) what the tension should be. Does it not just turn in to guess work and knowledge. How would you know if you were over tightening and putting spokes under more stress, thus leading to a wheel that will fail quicker?
Sorry if it sounds anal, But working in electronics manufacturing I know that a thermal difference of a few degrees outside of spec on a ceramic SMT capacitor will place thermal/mechanical stress on the component, and you wouldn't know about it until 6-12 months later. By this point the capacitor is leaky (takes time for a stress fracture to manifest) and has caused further damage to a electronic device.
Is this not the same? If someone at Giant quoted me 100kg per spoke then that is within Giants specs and tolerances. With no data available or from what I can find, how would buying a spoke tension tool help with no datum to compare it to?
Sorry if I went of topic, but just curious? Have eliminated all creaks now and spokes have a uniform sounding twang.0 -
One tip I had for wheel building without a spoke tension meter is to ping each spoke and make sure it produces the same tone. If your back wheel is the same build as your front that's probably a decent guide.
The sound and tension front to back are probably different due to different length spokes due to different flange sizes and offset due to discs, cassette, etc. Spokes on opposite sides of the same wheel will often have different tensions. So all of the spokes on the drive side rear should have equal tension, non drive side will probably be different but should all match each other. Front wheel again match tensions on each side.
In very simple terms higher tension gives a stronger wheel, until you go too far and break something that is. Rims are usually the limiting factor I believe. Look up the tension according to what rims you have. Then go close to the maximum tension on the side that needs to be tighter. The other side match the tensions at whatever they need to be to keep the wheel centred and true.
If tension is too low when the spoke is at the bottom of the wheel it becomes unloaded and can then loosen. Obviously this is a bad thing.0 -
Thankyou for the information. If said data is not available how would you know what to tension the spokes to?
I have got them running fairly true, and have tightened the nipples to eliminate the sound I was experiencing before. But how would I know if I was over tightening?
I do agree with something like park tools spoke tension gauge and the app that comes with it so you can see the spread of the tension. But you need the base tension for this to work. If you don't have the base tension how do you know you are setting the tension correctly?0 -
In very simple terms higher tension gives a stronger wheel, until you go too far and break something that is. Rims are usually the limiting factor I believe.
I disagree. There is no reason to go beyond 'tight enough', despite what is often quoted. Higher tension doesn't make for stiffer wheels either. What is 'tight enough' is another question though.0 -
I'm with Nick, any deflection adds tension to one side and removes it from the other, so where both sides spokes tension were before (as long as it was in the elastic deformation region, and the deflection doesn't take one in to plastic or the other sides out of elastic) doesn't affect it.Currently riding a Whyte T130C, X0 drivetrain, Magura Trail brakes converted to mixed wheel size (homebuilt wheels) with 140mm Fox 34 Rhythm and RP23 suspension. 12.2Kg.0
-
If the wheel stays true when you stress relieve it, it is still in elastic zone. Simple as that.
Higher tension does not make for higher stiffness, but it does make it stronger as the higher the tension, the higher the force the wheel can handle before spokes go loose, and spokes going loose is the only way a wheel can fail apart from localised forces that can bend the rim.
So yes, spoke tension is critical.
Good builders have a great feel for tension, but may still measure it, mainly to make sure that they don't go over the limits set by the hub flanges or rim pullout.
Spokes will never work themselves tighter during use, they can only loosen.
Tighter spokes have a far less tendency to loosen due to higher friction forces on the threads.
So higher strung wheels tend to be more reliable.0 -
Good builders have a great feel for tension, but may still measure it, mainly to make sure that they don't go over the limits set by the hub flanges or rim pullout.
I do agree with the last 3 posts, but my question still remains with no data available why would you use a spoke tension gauge to measure it, what are you comparing it to?
So if no data is available or hard to find, how would you know what the tension should be? I know the general rule of thumb is twang the spokes and if you have a high pitched sound then it is good. But this could lead to more permanent damage.
If you were to use this approach I could keep on using an uncalibrated ruler against another uncalibrated ruler, the next thing you know I now have a 2 foot member.0 -
In very simple terms higher tension gives a stronger wheel, until you go too far and break something that is. Rims are usually the limiting factor I believe.
I disagree. There is no reason to go beyond 'tight enough', despite what is often quoted. Higher tension doesn't make for stiffer wheels either. What is 'tight enough' is another question though.
I believe having even tension on each side is more important and a gauge will help you achieve this more accurately.
I'm no expert though, I've only built a few wheels and this is what I understand from reading various bits and pieces. Quite happy to be corrected and learn more as I go.0 -
[url=http://www.bikeradar.com/forums/viewtopic.php?p=19622488#p19622488]Clockworkmark31[/url] wrote:Good builders have a great feel for tension, but may still measure it, mainly to make sure that they don't go over the limits set by the hub flanges or rim pullout.
I do agree with the last 3 posts, but my question still remains with no data available why would you use a spoke tension gauge to measure it, what are you comparing it to?
So if no data is available or hard to find, how would you know what the tension should be? I know the general rule of thumb is twang the spokes and if you have a high pitched sound then it is good. But this could lead to more permanent damage.
If you were to use this approach I could keep on using an uncalibrated ruler against another uncalibrated ruler, the next thing you know I now have a 2 foot member.
Plenty of data available if you look for it or ask the manufacturer. For instance stans publish spoke tensions for all their rims on their website.0 -
[url=http://www.bikeradar.com/forums/viewtopic.php?p=19622488#p19622488]Clockworkmark31[/url] wrote:Good builders have a great feel for tension, but may still measure it, mainly to make sure that they don't go over the limits set by the hub flanges or rim pullout.
I do agree with the last 3 posts, but my question still remains with no data available why would you use a spoke tension gauge to measure it, what are you comparing it to?
So if no data is available or hard to find, how would you know what the tension should be? I know the general rule of thumb is twang the spokes and if you have a high pitched sound then it is good. But this could lead to more permanent damage.
I am asking if the data is unavailable then why would you use a spoke tension guide, what are you comparing the data to and how would you know that the spoke tension falls within the set parameters of the manufacturer. Yes I could call them and eventually find the information out, but if the information is not available and you have wheel builders saying it is ok, who is it ok with there own parameters or the parameters it was designed for?
There is no point in using a spoke tension gauge unless you have the data for what said wheel should be calibrated against.
It is a waste of time.
If you were to use this approach I could keep on using an uncalibrated ruler against another uncalibrated ruler, the next thing you know I now have a 2 foot member.
Plenty of data available if you look for it or ask the manufacturer. For instance stans publish spoke tensions for all their rims on their website.0 -
[url=http://www.bikeradar.com/forums/viewtopic.php?p=19622488#p19622488]Clockworkmark31[/url] wrote:Good builders have a great feel for tension, but may still measure it, mainly to make sure that they don't go over the limits set by the hub flanges or rim pullout.
I do agree with the last 3 posts, but my question still remains with no data available why would you use a spoke tension gauge to measure it, what are you comparing it to?
So if no data is available or hard to find, how would you know what the tension should be? I know the general rule of thumb is twang the spokes and if you have a high pitched sound then it is good. But this could lead to more permanent damage.
If you were to use this approach I could keep on using an uncalibrated ruler against another uncalibrated ruler, the next thing you know I now have a 2 foot member.
Plenty of data available if you look for it or ask the manufacturer. For instance stans publish spoke tensions for all their rims on their website.
I am asking if the data is unavailable then why would you use a spoke tension guide, what are you comparing the data to and how would you know that the spoke tension falls within the set parameters of the manufacturer. Yes I could call them and eventually find the information out, but if the information is not available and you have wheel builders saying it is ok, who is it ok with there own parameters or the parameters it was designed for?
There is no point in using a spoke tension gauge unless you have the data for what said wheel should be calibrated against.
It is a waste of time.0 -
wheel builders will use the information that is readily available and if it's not which is unlikely they'll use their experience on the construction of the rim.
Your argument is massively flawed, you say that there is no information, yet there is and argue that a tension gauge is useless without knowing the tension needed, which is perfectly true but that information is readily available.0 -
I do agree with the last 3 posts, but my question still remains with no data available why would you use a spoke tension gauge to measure it, what are you comparing it to?
The main thing you're looking for is even tension which requires no datum. However, you can calculate the appropriate range of tension for your spokes off of the chart provided with the tool. This will give you a range of appropriate tensions for the type of spoke you are running (converted as the spoke thickness of course effects the reading). Once you know this then its the application of common sense as to whether you might stick with that or adjust it up or down a little.A Flock of Birds
+ some other bikes.0 -
My spec for a front wheel is 1100N disc side, this is what is needed to keep the wheel stable in the long term without the need for truing (if it is done right). All MTB rims today can handle that tension (in fact they can handle 1200N some more). NDS is whatever it is to keep the wheel dished. Adding one full turn to each spoke is a lot and may have taken you beyond the tension limit of the rim or maybe not. No way to know without measuring the tension. Also adding one full turn to each spoke will have put the wheel out of dish if its a disc brake wheel.http://www.thecycleclinic.co.uk -wheel building and other stuff.0
-
I do agree with the last 3 posts, but my question still remains with no data available why would you use a spoke tension gauge to measure it, what are you comparing it to?
The main thing you're looking for is even tension which requires no datum. However, you can calculate the appropriate range of tension for your spokes off of the chart provided with the tool. This will give you a range of appropriate tensions for the type of spoke you are running (converted as the spoke thickness of course effects the reading). Once you know this then its the application of common sense as to whether you might stick with that or adjust it up or down a little.
Thank you,
This makes sense, I just couldn't see the point of a tension gauge with nothing to compare it to. But if you use to check for an even spread or general tension is even I get it.
As to the data being available let me tell you I have looked for it and had a chat with Giant and no data was given. This is why I was questioning what is the point of the gauge if you have no datum to compare it to.0 -
Giant don't make wheels though, look at some spoke and rim manufacturers sites and you'll see that for conventional parts the results are all pretty similar. Whether you use a gauge or the mkI eardrum, you still have to make sure they are tight 'enough' without being too tight.Currently riding a Whyte T130C, X0 drivetrain, Magura Trail brakes converted to mixed wheel size (homebuilt wheels) with 140mm Fox 34 Rhythm and RP23 suspension. 12.2Kg.0