Rant and blow off from work....what do do?
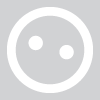
Clockworkmark31
Posts: 1,053
Hey all,
Getting frustrated in work atm, I'm an electronics engineer and have always worked in the field or somewhere I could make a difference.
This year I have started working in the manufacturing process (first for me) and have picked up general failures and why products fail (using 5 whys etc).
Now I seem to have come up against a brick wall. I work on the shop floor and can see things happening in real time and can react to it immediately and have built up my own network within my company - who will rectify the problem or give me guidance at a senior level etc, this was before a recent restructure.
Before a recent restructure I had the support and backup to rectify failures, the people who were backing me up have now been removed from the company, due to "adjusting to the market".
Now as an engineer I am getting frustrated, I see common problems over and over again but nothing changes. I can go back through the process and identify the issue and give suggestion on what changes need to be implemented. But because we have adopted to "lean manufacturing" everyone seems to be overlooking the fundamental flaws.
The focus has changed to quantity over quality and the "lean team" are putting pressure on TL's etc to make the process quicker rather than address the situation.
For me this is a bad practice, but everyone has been sold on this idea pretty much to MD level. For me it is bad practice and I keep getting overruled or ignored by the lean team when I pick out flaws in their system.
Question - do I just go to the MD and put this to them, or do I sit back and follow the changes that are clearly wrong and say nothing?
Getting frustrated in work atm, I'm an electronics engineer and have always worked in the field or somewhere I could make a difference.
This year I have started working in the manufacturing process (first for me) and have picked up general failures and why products fail (using 5 whys etc).
Now I seem to have come up against a brick wall. I work on the shop floor and can see things happening in real time and can react to it immediately and have built up my own network within my company - who will rectify the problem or give me guidance at a senior level etc, this was before a recent restructure.
Before a recent restructure I had the support and backup to rectify failures, the people who were backing me up have now been removed from the company, due to "adjusting to the market".
Now as an engineer I am getting frustrated, I see common problems over and over again but nothing changes. I can go back through the process and identify the issue and give suggestion on what changes need to be implemented. But because we have adopted to "lean manufacturing" everyone seems to be overlooking the fundamental flaws.
The focus has changed to quantity over quality and the "lean team" are putting pressure on TL's etc to make the process quicker rather than address the situation.
For me this is a bad practice, but everyone has been sold on this idea pretty much to MD level. For me it is bad practice and I keep getting overruled or ignored by the lean team when I pick out flaws in their system.
Question - do I just go to the MD and put this to them, or do I sit back and follow the changes that are clearly wrong and say nothing?
0
Comments
-
Bit more info, we have a graduate scheme in place and the people calling the shots atm are graduates or people that believe in Kaizen events etc, and have never worked in this industry.
Do I just sit back and let them implement systems that do not work "on paper they work" or do I go against them all and falsify their suggestions.
Ultimately they are playing with my future.0 -
The question you have to ask is we're the people removed because of their resistance to change (that's what it may be labeled as by management). If so, you are on dangerous ground and I would be updating my cv0
-
Toyota are famous for their lean manufacturing processes, and they proved that taking care of the small problems improves the overall picture. Toyota is one of the best examples of lean that others are still learning from. Do the "lean team" really understand lean manufacturing?
(Btw - before further comments - I also do not really understand lean!!)0 -
First reply is to Matthew;
Why do you think I am in dangerous grounds? I have not been opposed to changes and do welcome them -But when basic flaws get overlooked I can't see how skipping or inventing new processes to mask initial problems can work.
Surely this goes back to newton " for every action, there is an opposite and equal reaction"!
Bungaballs, I agree with what you are saying, Toyota is fantastic in this.
But from what I see, we identify a problem then overlook this and come up with an alternative to lead time etc.
All this ignores the principle issue that is causing failures.
I feel like I am trying to preach on deaf ears0 -
Clockworkmark31 wrote:First reply is to Matthew;
Why do you think I am in dangerous grounds? I have not been opposed to changes and do welcome them -But when basic flaws get overlooked I can't see how skipping or inventing new processes to mask initial problems can work.
Surely this goes back to newton " for every action, there is an opposite and equal reaction"!
Pointing out the flaws and possibly speaking to the MD has the danger that despite the right message they will kill the messenger, which they might have done to the people who where supportive to you.0 -
matthew h wrote:Clockworkmark31 wrote:First reply is to Matthew;
Why do you think I am in dangerous grounds? I have not been opposed to changes and do welcome them -But when basic flaws get overlooked I can't see how skipping or inventing new processes to mask initial problems can work.
Surely this goes back to newton " for every action, there is an opposite and equal reaction"!
Pointing out the flaws and possibly speaking to the MD has the danger that despite the right message they will kill the messenger, which they might have done to the people who where supportive to you.
It looks like you will have to sit back and let this one take its course. In the meantime keep doing your job well and keep an eye out for opportunities. I once got a promotion due to effectively carrying my manager who was out of their depth and not suited to their role. The customers asked for me to replace him so they were moved sideways. Just don't burn any bridges.0 -
Thanks for the replies. some good advice here.
But I think I may have blown it for myself already.
A new position is available in work, one that I can do and offer advice on daily, only I lack the "relevant paperwork". I expressed my interest in the job and got told we pulled out you cv and don't think you are right, "but if I get my way we will be having further conversations".
Didn't even get the chance to interview, even though I haven't formally submitted my application.
I was told this by a manager who is involved in lean etc, but I think because I challenged them a few times before I have now set a president for myself, I feel I will be blocked before given an opportunity.
So having a think today, I thought why not better yourself, and I would like to pull out the books again. But I am in a stalemate with myself, and hope we have people in the same situation or senior positions to guide me.
I know my job in electronics but I am classed as a Technician, for me I get more fun out of identifying the problem then finding the root course and then trying to implement a system to eliminate the problem happening again, can anyone recommend some courses I should be looking in to? I have already studied electronics, and whilst I am not a senior design engineer etc, I do like finding the fault then trying to eliminate it.
Too many courses are available and I am looking for a good all round course.
Any ideas?0 -
Also a couple of the people (from lean team) went to the same college as me, did the same level of training as me, but have got lucky or had a break in their career to get to a senior position. why would people forget this unless threatened. I don't see the point in taking sandwich placements etc when you have people who want to better themselves already in the company.0
-
matthew h wrote:Clockworkmark31 wrote:First reply is to Matthew;
Why do you think I am in dangerous grounds? I have not been opposed to changes and do welcome them -But when basic flaws get overlooked I can't see how skipping or inventing new processes to mask initial problems can work.
Surely this goes back to newton " for every action, there is an opposite and equal reaction"!
Pointing out the flaws and possibly speaking to the MD has the danger that despite the right message they will kill the messenger, which they might have done to the people who where supportive to you.
Why would a company do this, if you are trying to help the company? Maybe I am missing the link. But I would assume that anything, that could improve yield is a positive thing? So why would people want to stop this from happening? The only conclusion I can come to is, to keep their selves in a position within the company.0 -
Toyota are not a great company - they used to be. They have had four recalls in the past year!...take your pickelf on your holibobs....
jeez :roll:0 -
Sometimes companies do lean wrong, having a MD that doesn't get it and a poor IE/CI manager will put you in just this situation. Any lean organisations 'should' be using cross functional teams to look at the process, you need to get yourself on as many of these as you can, put up with the poor decisions and get yours into the discussion.
Poor quality leads to destruction or rework, these impact so many of the TIMWOOD wastes it's not even funny.
Again, the only way to influence a lean culture is to be involved, you don't have to live it every day but be part of their process. It is easy for lean teams to get blinkered by an edict from above to 'increase throughput', ask them how it impacts parts out the door.FCN 120 -
I spent years working in 'Lean Manufacturing' in the UK after training in Japan.
Lean will not work unless all the processes are running at optimal performance and this can only be achieved if the small issues and low level faults are recognised and rectified.
Too many companies now think Lean simply means not holding stock and operating a Just-in-time system. However, without carrying out the Kaizen activities and employing TQP/TQM philosophies they will soon come a cropper.
Clockworkman1 - If you feel he is approachable then I'd go to the MD and explain your concerns. However, if the lean team have influence then you may be on a sticky wicket and I'd start thinking about looking for a new job before this one eats you up.“Life has been unfaithful
And it all promised so so much”
Giant Trance 2 27.5 2016 ¦ Sonder Broken Road 2021¦ Giant Revolt Advanced 2 2019 ¦ Giant Toughtroad SLR 1 2019 ¦ Giant Anthem 3 2015 ¦ Specialized Myka Comp FSR 20090 -
the opposite argument is why would you want to work for a company who works like this?
the perks don't always stand with management/employers. they should be just as happy to keep good workers, if they don't judge you to be a good worker, go somehwere that does. work takes up too much of your life for it to be Sh!t.
i've just handed my notice in at the company that i've worked for for over 9 years as they've totally forgotten about the employees and we're all just numbers these days. Now they're actually begging me to stay, but they can forget it, i gave them plenty of chances0 -
This sounds exactly like the company I work for. I'm a mechanical engineer and have tried getting a process change through to fix porous castings but might as well bash my head against the wall.
I hate working in high volume manufacturing, theres so much BS in everything. I'm now looking to get back to bespoke machine design so I have control over my designs again.Transition Patrol - viewtopic.php?f=10017&t=130702350 -
FishFish wrote:Toyota are not a great company - they used to be. They have had four recalls in the past year!
My sister in law has a Toyota Yaris, it has been recalled four times in six years I believe. It still suffers from the same sensor breaking yearly causing engine problems despite being replaced at Toyota every year. Absolutely terrible.
If everyone's at the company is fixed at doing things the new way then your not going to be able to change them, so go with it.
Same with working for family business's, if you show them a much more efficient / cheaper / effective way of doing things even with proof, they usually prefer to do things the way they've 'been doing it for years' and keep bringing it up only annoys them.0 -
I had a friend, a colour chemist who worked for Ford in his first job. They had a problem with paint spray nozzles blocking and he investigated it and discovered that paint was not being mixed according to manufacturers instructions and this was the cause of the problem. He found the answer and they wouldn't hear him, despite solving the problem having been placed in his lap. Eventually he bypassed local management and went to the top. Local management had him dismissed and he went over a year unemployed, unable to get references until my [then] employer took him on after he explained why they would not get references for him. They wanted people like him as researchers who wouldn't be bullied into saying what the accountants wanted to hear. He stayed there over forty years and became known and respected within the company right round the world.
There is a great job waiting for you, but not within the company where you are now. By all means raise your concerns with your local management but if not heeded then avoid the blacklisting stage and start looking for a job where your skills are valued.0 -
Rampage7110 wrote:FishFish wrote:Toyota are not a great company - they used to be. They have had four recalls in the past year!
My sister in law has a Toyota Yaris, it has been recalled four times in six years I believe. It still suffers from the same sensor breaking yearly causing engine problems despite being replaced at Toyota every year. Absolutely terrible.
If everyone's at the company is fixed at doing things the new way then your not going to be able to change them, so go with it.
Same with working for family business's, if you show them a much more efficient / cheaper / effective way of doing things even with proof, they usually prefer to do things the way they've 'been doing it for years' and keep bringing it up only annoys them.
My sister worked for Toyota so got a hefty discount on new cars. She drove a Seat Ibiza instead. Says it all really.0 -
Clockworkmark31 wrote:
The focus has changed to quantity over quality and the "lean team" are putting pressure on TL's etc to make the process quicker rather than address the situation.
Remind your "lean team" that it's a waste to have to repeat work due to poor quality. The production line should get it right first time rather than churn out mistakes as quick as they can.
Also anyone on the Toyota shop floor had the rights to bring the entire factory to a halt if they spotted a flaw."The Prince of Wales is now the King of France" - Calton Kirby0 -
It's not just what you say / know but also how you say it - think about how you're getting your message across. If you're not seen as a team-player by your boss and his peers, then chances of promotion are slim.Make mine an Italian, with Campagnolo on the side..0
-
Electronics engineer here too....
Electronics and engineering in general are very undervalued and disrespected these days, companies are largely run by desk jockeys, most of whom have little or no technical knowledge at all, stupidity has become the acceptable norm.
Because technology has become so cheap and accessible, these people think electronic engineering is "simple" work, they don't listen, they think your exaggerating everything and getting through to them is near impossible.
They're stuck in their ways, they implement "changes" that meet targets and "KPI's", but really don't take into consideration the technical and practical aspects of what they're doing, they don't listen to you because you do "dirty work" and they're better than you because they have a degree in media studies or sports science.
They work in a world where all you need is BS and a big mouth to be successful.
The office bod mentality when it comes to solving issues/mistake is one of finding somebody to blame, publicly embarrassing them and then doing sweet FA about the root cause.
The more noise you make about the problems, the more your seen as a trouble maker. It's about keeping the status quo, the status quo got those people where they are, moving outside of this is something they see as dangerous, your making them look stupid with your knowledge/experience and the more you do this the more they'll put you down.
When I worked for a Japanese tier 1 supplier to the automotive industry, I had the same issues you describe. The company eventually shut down, but not before head office sent over some Japanese bosses to try and save the place, within 3 weeks they'd sacked the MD, sacked the quality manager and sacked half the office staff. Following this the Japanese replacements listened to the engineers and the maintenance team and things started to get sorted, but in the end the damage had already been done and the recession killed it off (2008).
If you want to do well in electronics, to be respected and paid a decent wage, you need to move to Scandinavia, Germany or Japan. In any those places, being an engineer is considered as highly as being a doctor.
When I went over to Sweden to do some work for Volvo, the way they treated me was a real shock to the system, they even gave me a young lad to carry my test equipment and assist with my work, it took me 3 days to stop him calling me "sir". Back home your looked down upon, you become a general dogsbody, moving desks, computers and filing cabinets for lazy office staff.
I'm now a desk bound engineer, little has changed, the idiots get promotions, the technical/intelligent people get put down and prevented from doing anything they're good at.
Last employer wanted a software developer, they asked for someone with a degree in a science (because of course theoretical physics make you a programmer) related subject, they employed a sports science graduate (Sports? Science? Programming? Really? I give up......).
But that's the mentality we face as engineers, the gateway to our career is guarded by insecure, stupid people, who will do anything they can to hold you back.0 -
I agree massively with the above!0
-
Quote
"Fight for your Highest attainable aim but never put up resistance in vain"
Hans Selye
regards
ILG0 -
Wow, it has been so long since I have visited my initial post that I forgot about it.
Anyway a quick update. MOARspeed is right on the money.
I am still with the same company and haven't progressed anywhere yet. When the Lean manager started they said I had good ideas and would get me involved in Kaizens etc (so far I have given my suggestions that have been used and I have attended no Kaizens).
Interestingly a manager from test R&D requested me when my line was shut down due to "lean money saving" (can we run on one shift) I went to the lab for over a month did all the work proved myself.
Then my line was starting again and I had one day of sick so got told I had made a bad impression and my line needs me now. So I had to go back to the line where I am now. I keep seeing people at various levels leaving the company and they are key members (some of which are trying to recruit me to their new companies) this I find flattering.
But I feel I am left in a dilemma, go with the money etc to a new company and face the unkown. Or stay with the same company with the new lean changes that I disagree with.
Because I am a young engineer I feel I am stuck between a rock and a rock. I can chase the money, or try to stay and progress with my current company who has the lab (and this will pay for itself in the future with experience).
How would other people handle being told to do a more demanding job for the same money and thinking you have a chance of change and then being moved back to your original position?
Two minds, chase the money....not better for the future or chase the experience and a better future.
Ps the lean manufacturing does not work, or it does...but we got told it would be continuous improvement since my first post on this I have not seen someone come back to monitor how things are working or could be improved.
To give you an example of the BS that I think is happening, we have a functional tester that can test a maximum of 160 PCBs per clocked hour. This is fact. So products produced per hour wont increase as they are limited.
But If i can increase production before the functional tester and say I have increased production by 50% (missing out until a certain point) this surely is BS in my opinion. As you are still limited by the tester. Why do people who don't know the industry progress on BS whilst people who know it get skipped over.
Do i stay for the chance I may get the experience in the lab or leave. All of the people who backed me have either left or been made to leave.0