Carbon make-up
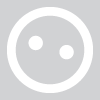
pesky_jones
Posts: 2,890
I was riding with someone the other day who is doing a degree in some type of dynamic engineering and his dissertation is making a carbon headtube or something or other... but this led onto talking about carbon in general.
He reckons the carbon criss-cross design is not as strong as the laminate type of design similar to how plywood is made etc. Its hard to explain but he thinks that the "criss-cross" pattern is purely for marketing purposes to shout "I'M CARBON" as such, and that the carbon fad is old so why not embrace the laminate option, which is not as aesthetically pleasing but stronger.
Anyone know much about this? Interesting to know whether it's true because I would of assumed any type of criss-cross laminate would be stronger then a parrallel laminate..if that makes sense.
He reckons the carbon criss-cross design is not as strong as the laminate type of design similar to how plywood is made etc. Its hard to explain but he thinks that the "criss-cross" pattern is purely for marketing purposes to shout "I'M CARBON" as such, and that the carbon fad is old so why not embrace the laminate option, which is not as aesthetically pleasing but stronger.
Anyone know much about this? Interesting to know whether it's true because I would of assumed any type of criss-cross laminate would be stronger then a parrallel laminate..if that makes sense.
0
Comments
-
A lot of it is just aesthetic. A frame will generally be made of lots and lots of unidirectional sheets, laid in different directions to maximise strenth/stiffness/weight as appropriate in different places.
You can use bidirectional, but can't optimise the layup in the same way. It's generally only used for a top coat, becuase like you say people associate carbon with that bidirection 'weave'. That said, it's far less common now than it used to be, and more are more companies are sticking with a unidirectional outer layer. You also get different 'tows' in the woven stuff - 3k is the most common - about 3mm per square, Scott used to use 12k, and some people use 1k, which is a much finer aesthetic. Again though, it's generally only the outermost layer.0 -
I think he's correct and as njee states, it's usually only the outer layer thats unidirectional. At least in frame design. A carbon brake disk for example will still be unidirectional though.Planet X Kaffenback 2
Giant Trance X2
Genesis High Latitude 2x10
Planet X n2a
Genesis Core 200 -
I mean bidirectional for the brake disk, doh!Planet X Kaffenback 2
Giant Trance X2
Genesis High Latitude 2x10
Planet X n2a
Genesis Core 200 -
There I was hoping that someone else had a fetish for carbon effect lipstick and eyeliner.0
-
The only argument for a weave top layer is that it slightly more resistant to impacts that could cause a minor delamination than a unidirectional top layer, but an aramid (Kevlar) weave is better still, I have seen arguments that titanium thread helps (As used by Pagani cars). though have no data to support it.
(3rd year project was impacts on CF plates for the US air force.......)Currently riding a Whyte T130C, X0 drivetrain, Magura Trail brakes converted to mixed wheel size (homebuilt wheels) with 140mm Fox 34 Rhythm and RP23 suspension. 12.2Kg.0 -
Awesome. Carbon fibre plates. Do they have titanium knives and forks?I don't do smileys.
There is no secret ingredient - Kung Fu Panda
London Calling on Facebook
Parktools0 -
Always wanted one of these:0
-
cooldad wrote:Awesome. Carbon fibre plates. Do they have titanium knives and forks?
I know some people that were born with a silver spoon0 -
Pesky Jones wrote:I was riding with someone the other day who is doing a degree in some type of dynamic engineering and his dissertation is making a carbon headtube or something or other... but this led onto talking about carbon in general.
He reckons the carbon criss-cross design is not as strong as the laminate type of design similar to how plywood is made etc. Its hard to explain but he thinks that the "criss-cross" pattern is purely for marketing purposes to shout "I'M CARBON" as such, and that the carbon fad is old so why not embrace the laminate option, which is not as aesthetically pleasing but stronger.
Anyone know much about this? Interesting to know whether it's true because I would have assumed any type of criss-cross laminate would be stronger then a parrallel laminate..if that makes sense.
what you see on a carbon frame is a Hero layer. IE somthing to look nice.
it has no relation to the actual construction or the frame.
just look at the people shock at the finish of the "bare" CF frames."Do not follow where the path may lead, Go instead where there is no path, and Leave a Trail."
Parktools :?:SheldonBrown0 -
cyd190468 wrote:The reason why they don't use woven sheet for the bulk of construction is that if you layer them the texture produces voids in the lamination the must be filled with resin. This produces a heavier product. That's why high end road frames are unidirectional all the way to the surface.
ONE possible reason. Not 'The reason'. In fact, no reason at all if you take care in making your assembly. :roll:
Unidirectional (UD) laminates are stronger and more durable than woven sheets. One key reason for this is that in a woven sheet, the weaving process introduces a crimp to the fibre and that crimp is a profound weakness. UD laminates are also thinner (which means less resin required). IME, UD laminates also have a prefferential Poissons ratio compared to woven. Woven stuff looks nice, hence it's use as a cosmetic outer layer. Unidirectional can look pretty messy before it's sheeted. UD is cheaper to buy as a pre-preg material and easier to lay up.
There are a chunk of provisos to this which I'm happy to discuss (the influence of cycle time vs UD and woven, pre-preg vs resin infusion etc), but what's above kinda sums things up in a bit of nutshell.
Beginner: A preffered method now to enhance impact protection on composites is to use a thermoplastic composites, as opposed to metallic interlayers or threads. Carbon/PPS systems are increasingly common now for wing leading edges and other aircrft frontal structures - offers approx 4x the impact performance of carbon/epoxy systems, but with a significant loss of stiffness. The loss of stiffness is giving us major headaches at the moment in terms of structural capability, so I'm still thinking that using a TPC outer set of layers over a TS compsoites is the way forward for automotive apps- there's a few applications that do this apperently, but the material suppliers won't give us details)How would I write my own epitaph? With a crayon - I'm not allowed anything I can sharpen to a sustainable point.
Disclaimer: Opinions expressed herein are worth exactly what you paid for them.0 -
Thanks for the Update, that work was back in the late 1980's so didn't expect it to be upto date, though 'costwise' it may be! Work I did was for the USAF and related to birdstrikes on F-16's, comparing net and inter layer stresses and with a UD top and weave top layers. we did a very small amount using aramid, but hadn't started to scratch that surface (ahem) when I graduated.Currently riding a Whyte T130C, X0 drivetrain, Magura Trail brakes converted to mixed wheel size (homebuilt wheels) with 140mm Fox 34 Rhythm and RP23 suspension. 12.2Kg.0
-
The Beginner wrote:Thanks for the Update, that work was back in the late 1980's so didn't expect it to be upto date, though 'costwise' it may be! Work I did was for the USAF and related to birdstrikes on F-16's, comparing net and inter layer stresses and with a UD top and weave top layers. we did a very small amount using aramid, but hadn't started to scratch that surface (ahem) when I graduated.
As a project goes, it's best described as 'whoa, dude!'
IIRC something similar may be coming in soon. If I could get the Centre to spring for an Ultrasonic microscope we'd be onto some really interesting research that'd follow on really nicely from your previous project work! Oh well, back to suspension arms until then!How would I write my own epitaph? With a crayon - I'm not allowed anything I can sharpen to a sustainable point.
Disclaimer: Opinions expressed herein are worth exactly what you paid for them.0 -
cyd190468 wrote:I was just trying to keep it simple for the OP as he obviously doesn't know much about composites.
I do know about composites, there was a huge one on dale farm wasnt there?0 -
Clank wrote:As a project goes, it's best described as 'whoa, dude!'
IIRC something similar may be coming in soon. If I could get the Centre to spring for an Ultrasonic microscope we'd be onto some really interesting research that'd follow on really nicely from your previous project work! Oh well, back to suspension arms until then!Currently riding a Whyte T130C, X0 drivetrain, Magura Trail brakes converted to mixed wheel size (homebuilt wheels) with 140mm Fox 34 Rhythm and RP23 suspension. 12.2Kg.0 -
cyd190468 wrote:No need for eye rolling I was just trying to keep it simple for the OP as he obviously doesn't know much about composites.
There's a big difference between simple and correct. Keep it accurate about materials/processes, I stop rolling eyes. Do we have an accord?
Plus if Pesky knew all about composites, he wouldn't have been asking a fair and interesting question, now would he?The Beginner wrote:Wasn't as much fun as it sounds......still fun though, I was the first person doing what was a rolling project so most my work was just perfecting how to make some plates, back in 1989 it wasn't that easy, all had to be peak of course.
PEEK? Holy cow, that stuff is difficult to work! We've got a few projects that have looked at aspect of machining that stuff - it is one tough S.O.B. (hence it's common use now for defence and aerospace, I guess!). There should be a new DMG turning up soon, specifically for that kind of project work, and it'll be loaded with some very interesting features.How would I write my own epitaph? With a crayon - I'm not allowed anything I can sharpen to a sustainable point.
Disclaimer: Opinions expressed herein are worth exactly what you paid for them.0 -
PEEK, but can you say it without googling it?
We use the stuff more and more now with electrical harnesses as protective coverings, as you say, it's tough sh1t.
Currently looking at a nice bit of laser marking kit so that we can mark our own ID plates.
All boring I mean good stuff!0 -
DodgeT wrote:PEEK, but can you say it without googling it?
We use the stuff more and more now with electrical harnesses as protective coverings, as you say, it's tough sh1t.
Currently looking at a nice bit of laser marking kit so that we can mark our own ID plates.
All boring I mean good stuff!
What wavelength? - may have some contacts depending on system requirements (just been pricing up new marking systems for our place).How would I write my own epitaph? With a crayon - I'm not allowed anything I can sharpen to a sustainable point.
Disclaimer: Opinions expressed herein are worth exactly what you paid for them.0