Advantage of handbuilt
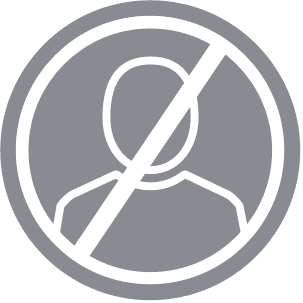
cheaterkiller
Posts: 159
What advantage does handbuilt wheels have over machine built wheels of the same price? Machines are generally far more precise.
0
Comments
-
1. You get to mix and match components to suit your requirements.
2. You can be sure that the parts are readily available for repairs/spares.
3. The wheel will be built with love and care, not done my a machine.
4. A handbuilt wheel will generally be repairable economically.
5. A machine will build each wheel to the same specification and tolerence, but is unlikely to be able to adjust things such as tension to cater for the inconsistency that invariably occurs in components. The wheelbuilder will fine tune each wheel to suit.Yellow is the new Black.0 -
cheaterkiller wrote:What advantage does handbuilt wheels have over machine built wheels of the same price? Machines are generally far more precise.
I'm just worried the machines may one day rise up against us - I saw a film like that once...0 -
I don't think there are any advantages really. I've had both and had few problems. Years ago people used to say that a hand built frame was the way to go. Hardly anyone orders and buys a handbuilt frame these days and the majority of frames that are raved about are made in Taiwan or somewhere similar.
Why buy a machine built frame and then criticise machine built wheels ? I just don't understand.0 -
cheaterkiller wrote:What advantage does handbuilt wheels have over machine built wheels of the same price? Machines are generally far more precise.
I guess it is the same with wheels. If you buy cheap wheels, you will get low spec machined parts that are built to average tolerances. If you buy high spec factory wheels then you would expect smaller tollerences and better quality materials as well as inspection.
Where hand-built comes in is more the artistic quality of the human eye, the personal attention to detail and the analogue approach to circles. What I mean is, if you can find a builder who takes pride in their work, who knows their stuff and who is having a good day - then you can get the personalised, individual level of buying advise, manufacturing and inspection that can only be archived by a skilled and trusted craftsman. The kind of 1 to 1 level of advise and quality control that comes from 1 human being caring about what they have built, that a factory has always strived (but has never been able to) achieve. Then again if they've got a hangover and are having a bad day ....Summer - Canyon Ultimate CF SLX 9.0 Team
Winter - Trek Madone 3.5 2012 with UDi2 upgrade.
For getting dirty - Moda Canon0 -
Most road wheels ie. Mavic, Campag, Shimano etc. are hand built, not machine built.0
-
themekon wrote:I don't think there are any advantages really. I've had both and had few problems. Years ago people used to say that a hand built frame was the way to go. Hardly anyone orders and buys a handbuilt frame these days and the majority of frames that are raved about are made in Taiwan or somewhere similar.
Why buy a machine built frame and then criticise machine built wheels ? I just don't understand.
Frames are built by people, not machines.0 -
themekon wrote:Flasher wrote:Most road wheels ie. Mavic, Campag, Shimano etc. are hand built, not machine built.
I appreciate that, just that in a lot of peoples eyes factory wheels mean some sort of production line and not the assumed attention to detail from the small wheel builder.
Here they are in the Campagnolo factory not paying any attention to detail http://www.youtube.com/watch?v=tIGm7pKx3rs
FWIW - there are some really ropey wheel builders out there who shouldn't even be allowed near a spoke key.0 -
themekon wrote:Flasher wrote:Most road wheels ie. Mavic, Campag, Shimano etc. are hand built, not machine built.
I appreciate that, just that in a lot of peoples eyes factory wheels mean some sort of production line and not the assumed attention to detail from the small wheel builder.
In reality, the only real distinction between quality handbuilts and quality factory built wheels is that the factory built ones are effectively designed as complete items with each component bespoke to the wheel whereas handbuilts are built up out of modular components. I think if factory wheels were always provided with readily available spares at an equivalent price to that of standard components then the market for handbuilts would become much narrower and more focussed (eg building wheels for particularly heavy or light riders).Faster than a tent.......0 -
styxd wrote:themekon wrote:I don't think there are any advantages really. I've had both and had few problems. Years ago people used to say that a hand built frame was the way to go. Hardly anyone orders and buys a handbuilt frame these days and the majority of frames that are raved about are made in Taiwan or somewhere similar.
Why buy a machine built frame and then criticise machine built wheels ? I just don't understand.
Frames are built by people, not machines.
Alright, by machine built I mean a mega long production line like in the Giant factory where the carbon fibre frames are placed in a mould.
The OP post was asking if there is any benefit from having hand built wheels not from a factory source . I don't think there is.0 -
I think Smidsy covered the practical advantages.
If both sets of wheels are, as the OP asked, the same price, then economies of scale and corporation profits and tax 'efficiency' and shareholders are to be weighed up against smaller overheads and the craftsman's need for profit.
It's also your choice as to who you want to give your money to?my isetta is a 300cc bike0 -
themekon wrote:Not in the traditional sense that I was referring to when it was thought by some that having a so called made to measure frame was the best thing to do.
The market is still there though I'm sure it has shrunk a bit. But you still find in the UK most cities having some options as to where to get a bespoke frame made and a number of carbon manufacturers do made to measure as well. But the thing is, most people don't actually need a made to measure frame because most people can be fitted perfectly well to standard frames. But if you can't - then made to measure is the best thing to do and probably always will be.
But that's not a good analogy with wheels anyway - a bike can be hand made without being made to measure and a wheel can be hand made without being specifically optimised to it's eventual rider.
And of course, criticising machine made wheels and not machine made frames is not inconsistent. The advantages of handmade wheels for people who (for example) ride all year round and weigh a lot are going to be very obvious when rim or spoke need replacing. If you never break spokes and don't wear rims out, then the advantages of handbuilt are much less.Faster than a tent.......0 -
Rolf F wrote:themekon wrote:Not in the traditional sense that I was referring to when it was thought by some that having a so called made to measure frame was the best thing to do.
The market is still there though I'm sure it has shrunk a bit. But you still find in the UK most cities having some options as to where to get a bespoke frame made and a number of carbon manufacturers do made to measure as well. But the thing is, most people don't actually need a made to measure frame because most people can be fitted perfectly well to standard frames. But if you can't - then made to measure is the best thing to do and probably always will be.
But that's not a good analogy with wheels anyway - a bike can be hand made without being made to measure and a wheel can be hand made without being specifically optimised to it's eventual rider.
And of course, criticising machine made wheels and not machine made frames is not inconsistent. The advantages of handmade wheels for people who (for example) ride all year round and weigh a lot are going to be very obvious when rim or spoke need replacing. If you never break spokes and don't wear rims out, then the advantages of handbuilt are much less.
The market for Bespoke is actually growing, not shrinking... we have tipped the bottom earlier... more and more independent workshops are popping up.
Re accuracy: I often go to GE Aviation in Caerphilly for work.. they overhaul GE and Rolls Royce Jet Engine for regular maintenance and repairs, great place to be if you like engineering. The final operation when the turbo fan is placed needs the fan to be balanced, like a car wheel, but with a lot more accuracy. A computer predicts where the weights should go by data coming from spinning, but the final touches are done by experienced technicians, as the computer cannot get the same level of accuracy. I think this says a lot and closes the argument of man Vs machineleft the forum March 20230 -
ugo.santalucia wrote:I think this says a lot and closes the argument of man Vs machine
Absolutely. Entirely irrelevantly, but something you will probably know but interesting anyway, I once visited AETC Turbines in Yeadon. Now there is some nice engineering but the bloke who was showing me what they did was saying that turbine blades used in power stations in the remoter parts of Canada and Alaska where built to higher standards than those used in airliners simply because the airline blades are checked far more frequently. Lovely things turbine blades - especially the single crystal grown ones.Faster than a tent.......0 -
Rolf F wrote:ugo.santalucia wrote:I think this says a lot and closes the argument of man Vs machine
Absolutely. Entirely irrelevantly, but something you will probably know but interesting anyway, I once visited AETC Turbines in Yeadon. Now there is some nice engineering but the bloke who was showing me what they did was saying that turbine blades used in power stations in the remoter parts of Canada and Alaska where built to higher standards than those used in airliners simply because the airline blades are checked far more frequently. Lovely things turbine blades - especially the single crystal grown ones.
Indeed...
I was talking about the fan though, which is at the front of the engine, the one that greets you when you board a budget flight, that's typically made of titanium or composite, depending on the manufacturer and it is a heavy beast, very hard to balance. It is way bigger than the rest of the engine as most of the air intake is actually redirected outside the compressor/turbine system... it is called bypass ratio, modern engines work with 15-20/1 bypass ratios
Turbine blades are made of various nickel super alloys, investment cast in a Bridgeman furnace to grow a single crystal microstructure, machined and then coated with 4 layers of various ceramic and intermetallic alloys to improve creep resistance. They are very tiny and machining accuracy and balance are less of an issue for those
NOW THIS is off-topic...left the forum March 20230 -
I get to pick what colour nipples I want. What more reason do you need to go hand built?0
-
ugo.santalucia wrote:Rolf F wrote:ugo.santalucia wrote:I think this says a lot and closes the argument of man Vs machine
Absolutely. Entirely irrelevantly, but something you will probably know but interesting anyway, I once visited AETC Turbines in Yeadon. Now there is some nice engineering but the bloke who was showing me what they did was saying that turbine blades used in power stations in the remoter parts of Canada and Alaska where built to higher standards than those used in airliners simply because the airline blades are checked far more frequently. Lovely things turbine blades - especially the single crystal grown ones.
Indeed...
I was talking about the fan though, which is at the front of the engine, the one that greets you when you board a budget flight, that's typically made of titanium or composite, depending on the manufacturer and it is a heavy beast, very hard to balance. It is way bigger than the rest of the engine as most of the air intake is actually redirected outside the compressor/turbine system... it is called bypass ratio, modern engines work with 15-20/1 bypass ratios
Turbine blades are made of various nickel super alloys, investment cast in a Bridgeman furnace to grow a single crystal microstructure, machined and then coated with 4 layers of various ceramic and intermetallic alloys to improve creep resistance. They are very tiny and machining accuracy and balance are less of an issue for those
NOW THIS is off-topic...
Nothing wrong with OT! I saw some of the single crystal ones. They told me that the RAF used conventionally cast turbine blades - only the Saudi airforce (presumably of the places they supplied) fitted all its aircraft with single crystal blades!Faster than a tent.......0 -
Rolf F wrote:ugo.santalucia wrote:Rolf F wrote:ugo.santalucia wrote:I think this says a lot and closes the argument of man Vs machine
Absolutely. Entirely irrelevantly, but something you will probably know but interesting anyway, I once visited AETC Turbines in Yeadon. Now there is some nice engineering but the bloke who was showing me what they did was saying that turbine blades used in power stations in the remoter parts of Canada and Alaska where built to higher standards than those used in airliners simply because the airline blades are checked far more frequently. Lovely things turbine blades - especially the single crystal grown ones.
Indeed...
I was talking about the fan though, which is at the front of the engine, the one that greets you when you board a budget flight, that's typically made of titanium or composite, depending on the manufacturer and it is a heavy beast, very hard to balance. It is way bigger than the rest of the engine as most of the air intake is actually redirected outside the compressor/turbine system... it is called bypass ratio, modern engines work with 15-20/1 bypass ratios
Turbine blades are made of various nickel super alloys, investment cast in a Bridgeman furnace to grow a single crystal microstructure, machined and then coated with 4 layers of various ceramic and intermetallic alloys to improve creep resistance. They are very tiny and machining accuracy and balance are less of an issue for those
NOW THIS is off-topic...
Nothing wrong with OT! I saw some of the single crystal ones. They told me that the RAF used conventionally cast turbine blades - only the Saudi airforce (presumably of the places they supplied) fitted all its aircraft with single crystal blades!left the forum March 20230 -
iPete wrote:I get to pick what colour nipples I want. What more reason do you need to go hand built?
..I think that closes the thread!0 -
ugo.santalucia wrote:Rolf F wrote:ugo.santalucia wrote:Rolf F wrote:ugo.santalucia wrote:I think this says a lot and closes the argument of man Vs machine
Absolutely. Entirely irrelevantly, but something you will probably know but interesting anyway, I once visited AETC Turbines in Yeadon. Now there is some nice engineering but the bloke who was showing me what they did was saying that turbine blades used in power stations in the remoter parts of Canada and Alaska where built to higher standards than those used in airliners simply because the airline blades are checked far more frequently. Lovely things turbine blades - especially the single crystal grown ones.
Indeed...
I was talking about the fan though, which is at the front of the engine, the one that greets you when you board a budget flight, that's typically made of titanium or composite, depending on the manufacturer and it is a heavy beast, very hard to balance. It is way bigger than the rest of the engine as most of the air intake is actually redirected outside the compressor/turbine system... it is called bypass ratio, modern engines work with 15-20/1 bypass ratios
Turbine blades are made of various nickel super alloys, investment cast in a Bridgeman furnace to grow a single crystal microstructure, machined and then coated with 4 layers of various ceramic and intermetallic alloys to improve creep resistance. They are very tiny and machining accuracy and balance are less of an issue for those
NOW THIS is off-topic...
Nothing wrong with OT! I saw some of the single crystal ones. They told me that the RAF used conventionally cast turbine blades - only the Saudi airforce (presumably of the places they supplied) fitted all its aircraft with single crystal blades!
The company that my Dad used to work for poineered single crystal turbine blades. It's quite old technology and isn't used that much any more.Science adjusts it’s beliefs based on what’s observed.
Faith is the denial of observation so that Belief can be preserved0