QI
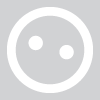
2Phat4Rapha
Posts: 238
Bin men wouldn’t take a discarded rim so thought I’d scrunch it into something they wouldn’t notice. Despite the ding in the side it was, reassuringly, darn impossible to squash it across its diameter. Taco-ing it wasn’t that easy either which was surprising but once done I got a separation. What amazed me was just how easy it was to then “wishbone” it by pulling apart the break. It was like tin foil.
No particular point to this other than I found it quite interesting.
No particular point to this other than I found it quite interesting.

I may be a minority of one but that doesn't prevent me from being right.
http://www.dalynchi.com
http://www.dalynchi.com
0
Comments
-
Thats Engineering for you.
The material used can be realy thin but its the shape & profile that gives it strength.
Another example is RSJ's (reenforced steel joist OR 'i beam'):
You can have an RSJ with circular cutout's running down the spine of the beam, this saves weight & materials, and its only a fraction weaker, than an RSJ with a solid spine (or without circular cutouts)
A circle is a strong shape.0 -
Rims used to be simply plugged together at the join, and could be pulled apart by hand. The welding (and machining) now used only serves to prevent a step in the braking track, and has no structural purpose.
It's been shown that a wheel whose rim is composed of 36 (or whatever) separate pieces, simply abutting one another (without interlocking), would function perfectly normally – perhaps surprisingly: this is because each "join" experiences only compression.0