fitting an alloy stem to a carbon fork
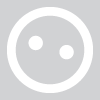
speedy21
Posts: 153
hi all , il try and explain this the best i can, i have carbon forks and i need to put an alloy stem onto them, the stem says 6Nm (i understand what Nm and torque wrench etc), but some stems say 5Nm or 7Nm etc. what i dont understand is that whoever makes the stem (FSA in this case) does not know what forks its going to be attached to and therefore does not know how strong the forks will be, so how can the Nm rating be put on the stem. shouldnt the fork say the Nm rating. what if the forks can only take 5Nm but the stem i buy says 7Nm. does anyone understand what im trying to say?????
if so an explanation would be great as i obviously dont want to crush my forks and i dont really want the handlebars coming off when im spinning down the road
fanx
if so an explanation would be great as i obviously dont want to crush my forks and i dont really want the handlebars coming off when im spinning down the road

0
Comments
-
speedy21 wrote:hi all , il try and explain this the best i can, i have carbon forks and i need to put an alloy stem onto them, the stem says 6Nm (i understand what Nm and torque wrench etc), but some stems say 5Nm or 7Nm etc. what i dont understand is that whoever makes the stem (FSA in this case) does not know what forks its going to be attached to and therefore does not know how strong the forks will be, so how can the Nm rating be put on the stem. shouldnt the fork say the Nm rating. what if the forks can only take 5Nm but the stem i buy says 7Nm. does anyone understand what im trying to say?????
if so an explanation would be great as i obviously dont want to crush my forks and i dont really want the handlebars coming off when im spinning down the roadfanx
You're probably over reacting a bit. If you're unsure what to do, tighten to the recommended setting. I can't see this being a problem. Should stay tight and work well. FWIW I was using a carbon seat post a while back and it tended to slip if I didn't tighten it really tight(no torque wrench). It never broke under repeated very tight clamping and unclamping. If you don't trust what the torque setting says or don't have faith in a carbon
steer tube, then switch to a metal steerer and you can crank on that hex key till the cows come home, without problems. I don't know what kind of torque settings these kind of things are built to withstand but it's probably way, way more than the recommended one. It had better be.0 -
your kindof gettin what im askin but not quite, i have faith in the carbon steerer (im thinking this is the very top of the forks that i clamp the stem onto??) what i want to know is what is the recommended setting for the forks. the stem doesnt come from the same manufacturer even so they wouldnt know.
are you maybe saying that the 6Nm is maybe a ball park figure that all forks are tightened to/or can withstand and that is why its printed on the stem, because that would be acceptable pressure for any carbon fork???0 -
This post addresses a similar issueyoungs_modulus wrote:Obviously, you're wondering how much you can crank on your seatpost clamp bolt(s) without crushing the carbon rails. Frankly, I wouldn't worry about it. I've never heard of anyone crushing carbon saddle rails before (breaking, yes, but not crushing in a clamp). Besides, the carbon rails are either very thick-walled or solid; either condition would make it harder to crush the carbon than, say, a thin-walled titanium tube. Just tighten your seatpost clamp until it doesn't slip and be done with it.
Lots of consumers take specified torque as gospel, but it's much less exact than some people think. The concept of "maximum torque" is really a stand-in for maximum clamping force. The relationship between applied torque and resulting clamping force depends on lots of things, especially these three: Mechanism design, thread pitch and lubrication (or the lack thereof). I'll discuss these in more detail:
- Mechanism design: Depending on how the saddle clamp is designed, you can generate lots of clamping force or relatively little from a given amount of torque. For example, a Campagnolo Record seatpost uses a single bolt, and the clamping force has essentially a 1:1 ratio with the force applied by tightening the bolt. On the other hand, the USE Alien post has a unique clamp design (they call it the "cyclops" clamp) that generates a lot of clamping force with just a little torque. I'm just guessing here, but it might be a ratio of 3:1 or 4:1. If I recall correctly, the Campy post has an M8 bolt while the USE post has an M5 bolt. Even if I got the bolt sizes wrong, you get the idea: the Campy post has a much beefier bolt because it needs a relatively high amount of torque to clamp tightly; the USE post has a much smaller bolt because it generates a similar clamping force with less applied torque.
- Thread pitch: A finer thread will generate a lot more clamping force than a coarser one. Many seatposts use M6 bolts; these have a thread pitch of one thread per millimeter (10 thread peaks or valleys per cm); M8 bolts have either 1 or 1.25 mm between each thread (8 or 10 threads/cm); M5 bolts have a 0.8mm thread pitch (12.5 threads/cm); finally, M4 bolts have a 0.7mm thread pitch (~14 threads/cm). The finer the thread pitch, the more clamping force you get for a given torque. My Ritchey WCS stem uses M4-threaded bolts and specifies a max applied torque of 5 N-m. That generates a higher clamping force than my old 3T stem which used M5 bolts and also specified a max torque of 5 N-m.
- Lubrication: This sounds obvious, but lots of people miss it: a lubed bolt tightens more easily than a dry bolt. If you apply 5 N-m to a dry bolt, it will stop turning when the friction force generated by the bolt's threads turning against the female threads creates a reaction torque of 5 N-m. If you lube the threads, the friction doesn't ramp up as fast as it did with the dry bolt, and so you get more clamping force for the same amount of applied torque. If you lube the threads but not the underside of the bolt head, you will get significantly less clamping force than you would have if you lubed up all the contact surfaces. A dry bolt head against a dry surface will generate lots of friction and stop your bolt from turning.
It's safe to assume that manufacturers' torque specs are for fully lubricated bolts and threads. (It doesn't take much grease to make a bolt "fully lubricated.")
As you can see, a torque spec takes into account lots of different variables. While an engineer can control the clamping mechanism and the thread pitch, the lubrication aspect is fairly variable. Some of my engineering work has involved aircraft control systems; these are parts in which improperly tightened bolts could cause a loss of control and a crash. In order to make sure I'm getting a certain clamping force in a bolted joint, I'll sometimes specify a number of turns after contact. If I have a clamp closed by an M6x1mm bolt, I might want that clamp to close by 3.5mm in order to be fully tightened. In this case, I would specify 3.5 turns after contact. (The bolt has a 1mm thread pitch, so each turn moves the bolt by 1mm).
Even the "number of turns" (NoT is the acronym I just made up) approach is imperfect...if my clamp is designed right but the part it's clamping is slightly undersized, the specified NoT won't produce enough clamping force. Tightening the bolt to a specified torque would produce more clamping force on the undersized part (whether it's "enough" is a separate question) than tightening to a specified NoT. Because a stem manufacturer can't assume what brand and model of handlebar might be bolted into his stem, torque specs make more sense than NoT specs.
You can make this as complicated as you like: e.g., bolted joints with are more flexible with Ti bolts than they are with steel bolts, which can affect how much clamping force is developed.
The point is that torque specs are not purely objective. Rather, they're approximations that include lots of assumptions. That said, I'm glad that more manufacturers are making them available.
Cheers,
Jason0 -
thanks for both answers guys, so basically if i do what it says on the stem im not gona do any damage and theyl stay on fine?
i wanted to make sure cos im planning on changing the stem and i dont wana rely on my lbs everytime i wana do something, could be costly,especially as i didnt buy the bike there.
thanks for your help guys
p.s. il be back will more stupid questions so keep your eyes pealed0 -
I use a Ritchey Torque Key for all clamp fittings, it's set at 5Nm's (supposedly). If it slips at that (never has, yet), then I'd use CF paste.Start with a budget, finish with a mortgage!0
-
I doubt if you need to go anywhere near 5 or 6nm to clamp a stem, both of those figures are bleedin tight. Personally I would forget the torque wrench and just go by feel with an Allen key, unless you are a complete ham fist with hands like shovels you will be well within limits.0
-
the torque rating is a limit not a suggestion, set the wrench to the suggested limit and then just tighten to what feels sufficently tight, you'll probably feel this is below the limit as SJ suggested.
I've got an alloy FSA stem connected to an alloy steerer on one end and carbon bars on the other, never had a problem with the bars getting crushed.
If you're really worried about the carbon steerer then it's probably best to get in contact with the manufacturer and find out the rating from them.0 -
-
Sh!t me, I've got to reply, I'm in agreement with Red!!!!
Materials, construction, design etc of the stem, or other component being clamped, will determine clamping force. For example, clamping tin foil at 5NM will destroy tin foil and apply 100%of force to steerer, clamping square cut cast iron at 5NM will apply 0% of force to steerer and not deform the cast iron at all.
(Figures at this time of evening may not be correct but u get the idea!)0